کد مقاله | کد نشریه | سال انتشار | مقاله انگلیسی | نسخه تمام متن |
---|---|---|---|---|
778308 | 1463788 | 2012 | 15 صفحه PDF | دانلود رایگان |
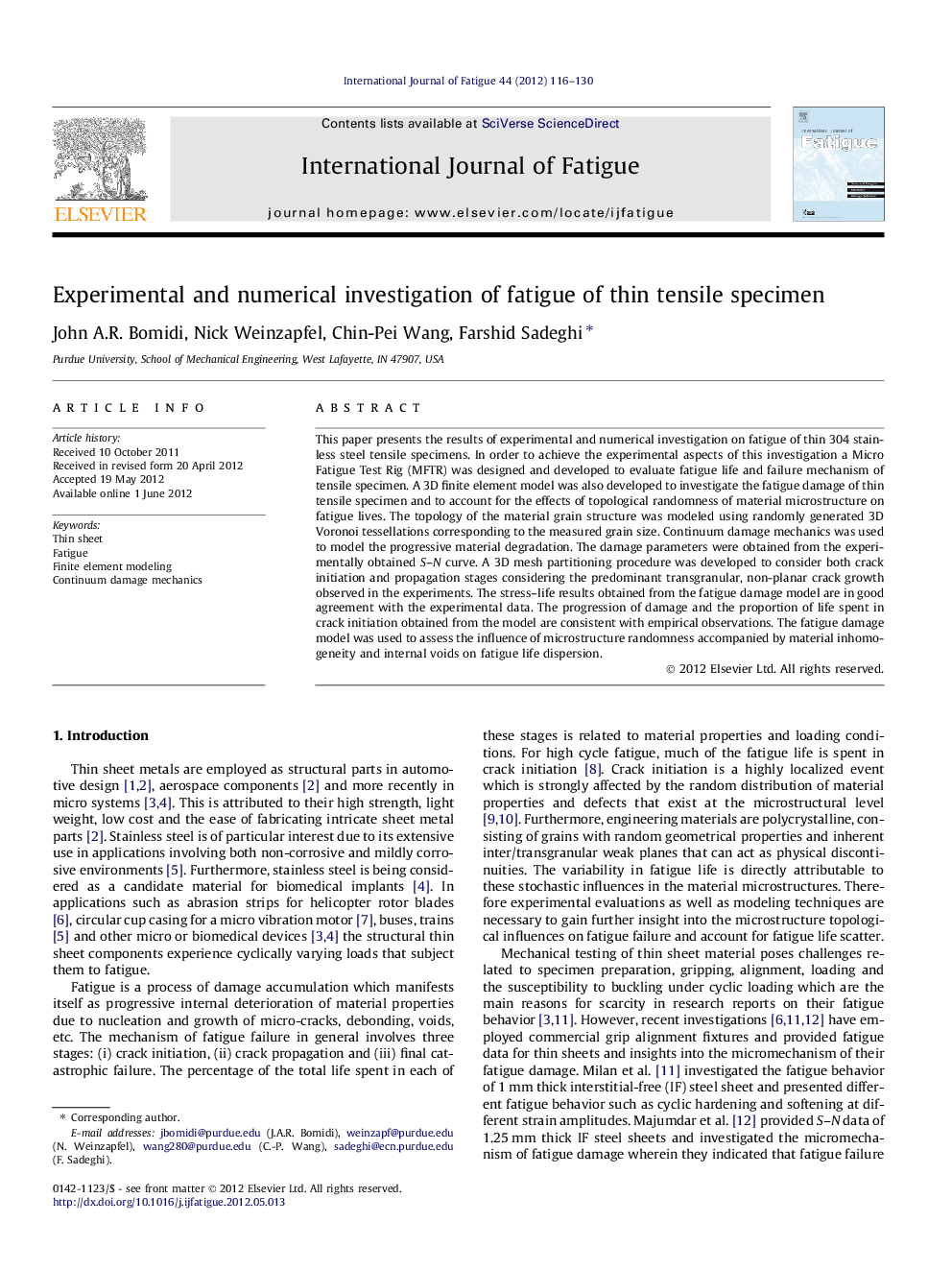
This paper presents the results of experimental and numerical investigation on fatigue of thin 304 stainless steel tensile specimens. In order to achieve the experimental aspects of this investigation a Micro Fatigue Test Rig (MFTR) was designed and developed to evaluate fatigue life and failure mechanism of tensile specimen. A 3D finite element model was also developed to investigate the fatigue damage of thin tensile specimen and to account for the effects of topological randomness of material microstructure on fatigue lives. The topology of the material grain structure was modeled using randomly generated 3D Voronoi tessellations corresponding to the measured grain size. Continuum damage mechanics was used to model the progressive material degradation. The damage parameters were obtained from the experimentally obtained S–N curve. A 3D mesh partitioning procedure was developed to consider both crack initiation and propagation stages considering the predominant transgranular, non-planar crack growth observed in the experiments. The stress–life results obtained from the fatigue damage model are in good agreement with the experimental data. The progression of damage and the proportion of life spent in crack initiation obtained from the model are consistent with empirical observations. The fatigue damage model was used to assess the influence of microstructure randomness accompanied by material inhomogeneity and internal voids on fatigue life dispersion.
► Developed a Micro Fatigue Test Rig to provide S–N data for thin tensile specimen.
► Crack initiation, transgranular crack growth and final separation observed for 304 SS.
► Developed a 3D FE damage model with a Mesh Partitioning procedure for crack growth.
► Accurately predicted proportion of life spent in crack initiation and damage progression.
► Demonstrated model’s applicability to study effects of material microstructure topology.
Journal: International Journal of Fatigue - Volume 44, November 2012, Pages 116–130