کد مقاله | کد نشریه | سال انتشار | مقاله انگلیسی | نسخه تمام متن |
---|---|---|---|---|
8943316 | 1645144 | 2019 | 24 صفحه PDF | دانلود رایگان |
عنوان انگلیسی مقاله ISI
3D extrusion printing of magnesium aluminate spinel ceramic parts using thermally induced gelation of methyl cellulose
دانلود مقاله + سفارش ترجمه
دانلود مقاله ISI انگلیسی
رایگان برای ایرانیان
کلمات کلیدی
موضوعات مرتبط
مهندسی و علوم پایه
مهندسی مواد
فلزات و آلیاژها
پیش نمایش صفحه اول مقاله
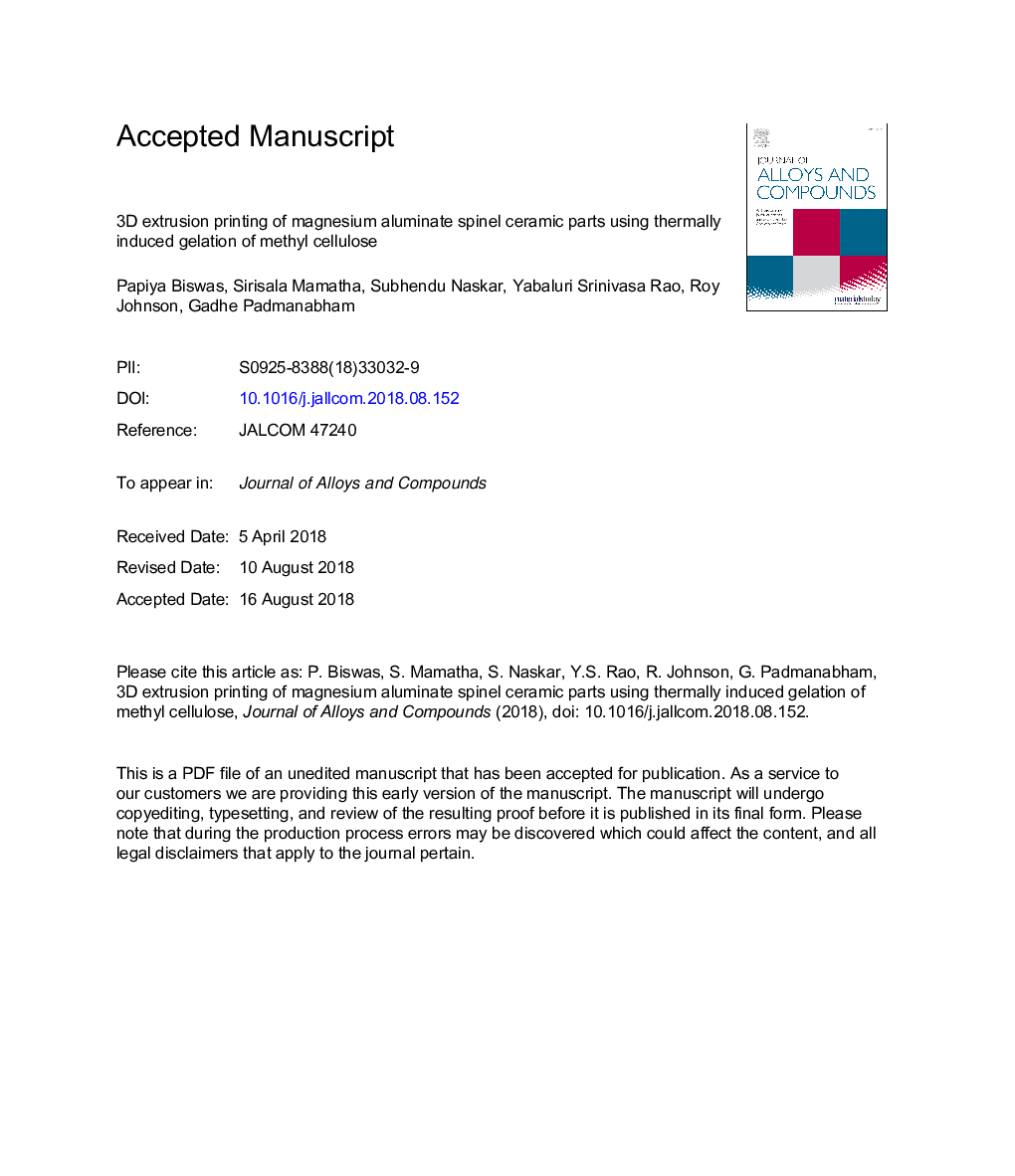
چکیده انگلیسی
Additive manufacturing (AM) is an innovative complex shaping technique with unlimited freedom and flexibility in fabrication. Though the majority of AM processes were focused in polymers, it is later extended to metals and very recently to ceramics. Conventional prototyping of ceramics, especially complex parts proceeds through several iterations of design and fabrication of dies, moulds, fixtures etc. which are cost intensive and also time taking to arrive at the final designs. Often the finished parts also needs machining to achieve the micro-features. 3D printing of ceramics with its inherent advantages simplifies above issues especially for fabrication of prototypes leading to the selection of optimum designs in a very short time. Further, as the same infrastructure is based on the printing of ceramic shapes using software generated virtual images it also results in lower cost. In the present study, unlike generally employed UV or visible curable resins to 3D print the green ceramic parts, a new concept of thermally induced gelation of methyl cellulose is used to retain the shape while printing of the parts. In this process, magnesium aluminate spinel paste formulated with 0.25% by weight of methyl cellulose (MC) having optimized rheology was 3D printed simultaneously exposing to the hot air flow close to the MC gelation temperature. Magnesium aluminate spinel test specimens are also shaped using generally practiced slip casting process for the sake of comparison, as slip casting process is not adaptable to fabricate the parts micro-features 3D printed in the present study. The formed parts by both the techniques were pressureless sintered at 1650â¯Â°C. 3D printed spinel specimens have shown comparable density, hardness and flexural strength with respect to the slip cast specimens complemented by fractographic analysis.
ناشر
Database: Elsevier - ScienceDirect (ساینس دایرکت)
Journal: Journal of Alloys and Compounds - Volume 770, 5 January 2019, Pages 419-423
Journal: Journal of Alloys and Compounds - Volume 770, 5 January 2019, Pages 419-423
نویسندگان
Papiya Biswas, Sirisala Mamatha, Subhendu Naskar, Yabaluri Srinivasa Rao, Roy Johnson, Gadhe Padmanabham,