کد مقاله | کد نشریه | سال انتشار | مقاله انگلیسی | نسخه تمام متن |
---|---|---|---|---|
1642488 | 1517232 | 2015 | 4 صفحه PDF | دانلود رایگان |
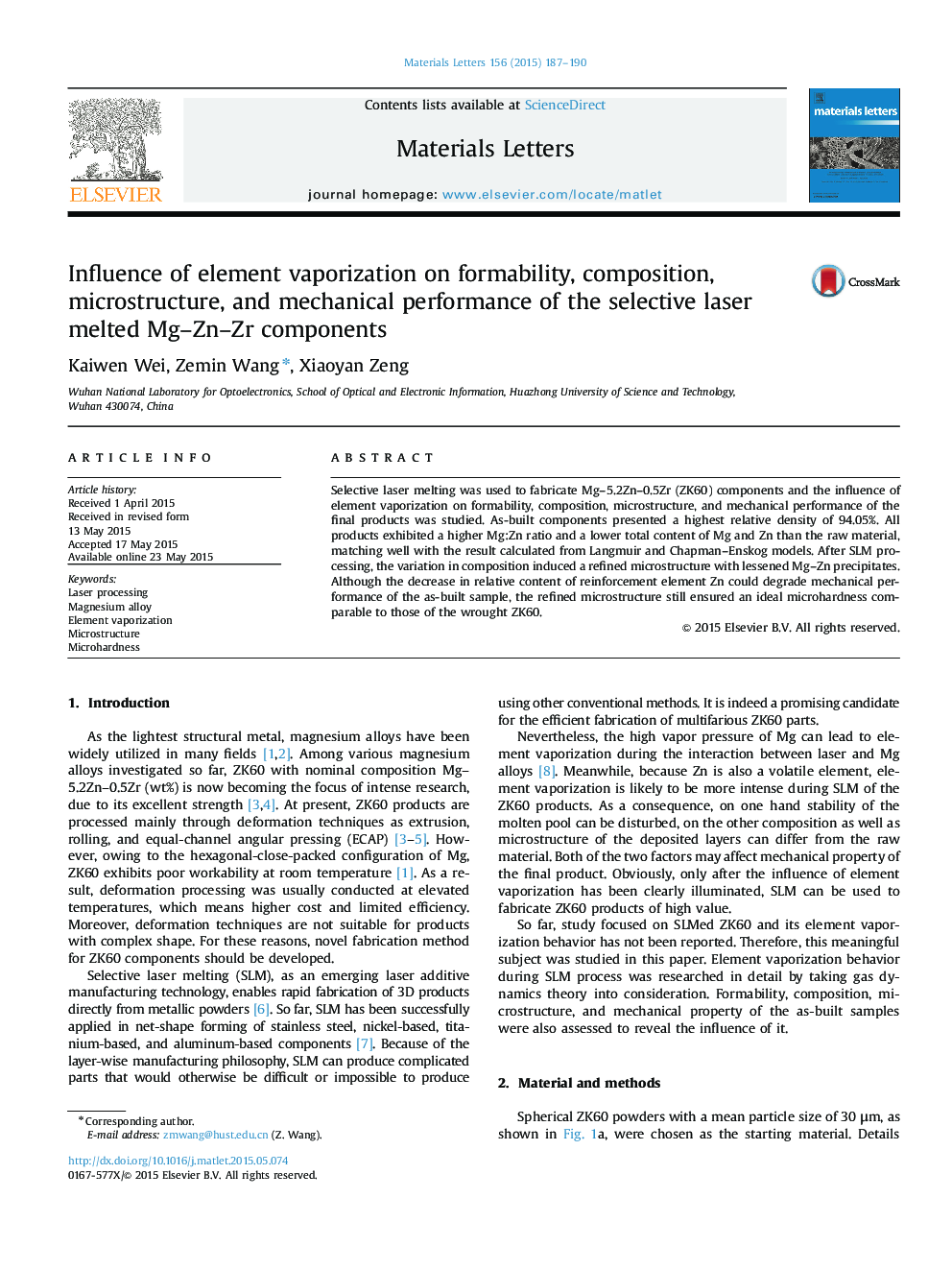
• Mg–Zn–Zr part with an ideal hardness was fabricated by selective laser melting.
• As-built part presented a higher Mg:Zn ratio due to element vaporization.
• Change in composition led to refined microstructure and lessened intermetallics.
• As-built part exhibited a highest relative density of 94.05%.
Selective laser melting was used to fabricate Mg–5.2Zn–0.5Zr (ZK60) components and the influence of element vaporization on formability, composition, microstructure, and mechanical performance of the final products was studied. As-built components presented a highest relative density of 94.05%. All products exhibited a higher Mg:Zn ratio and a lower total content of Mg and Zn than the raw material, matching well with the result calculated from Langmuir and Chapman–Enskog models. After SLM processing, the variation in composition induced a refined microstructure with lessened Mg–Zn precipitates. Although the decrease in relative content of reinforcement element Zn could degrade mechanical performance of the as-built sample, the refined microstructure still ensured an ideal microhardness comparable to those of the wrought ZK60.
Journal: Materials Letters - Volume 156, 1 October 2015, Pages 187–190