کد مقاله | کد نشریه | سال انتشار | مقاله انگلیسی | نسخه تمام متن |
---|---|---|---|---|
1707318 | 1012543 | 2006 | 13 صفحه PDF | دانلود رایگان |
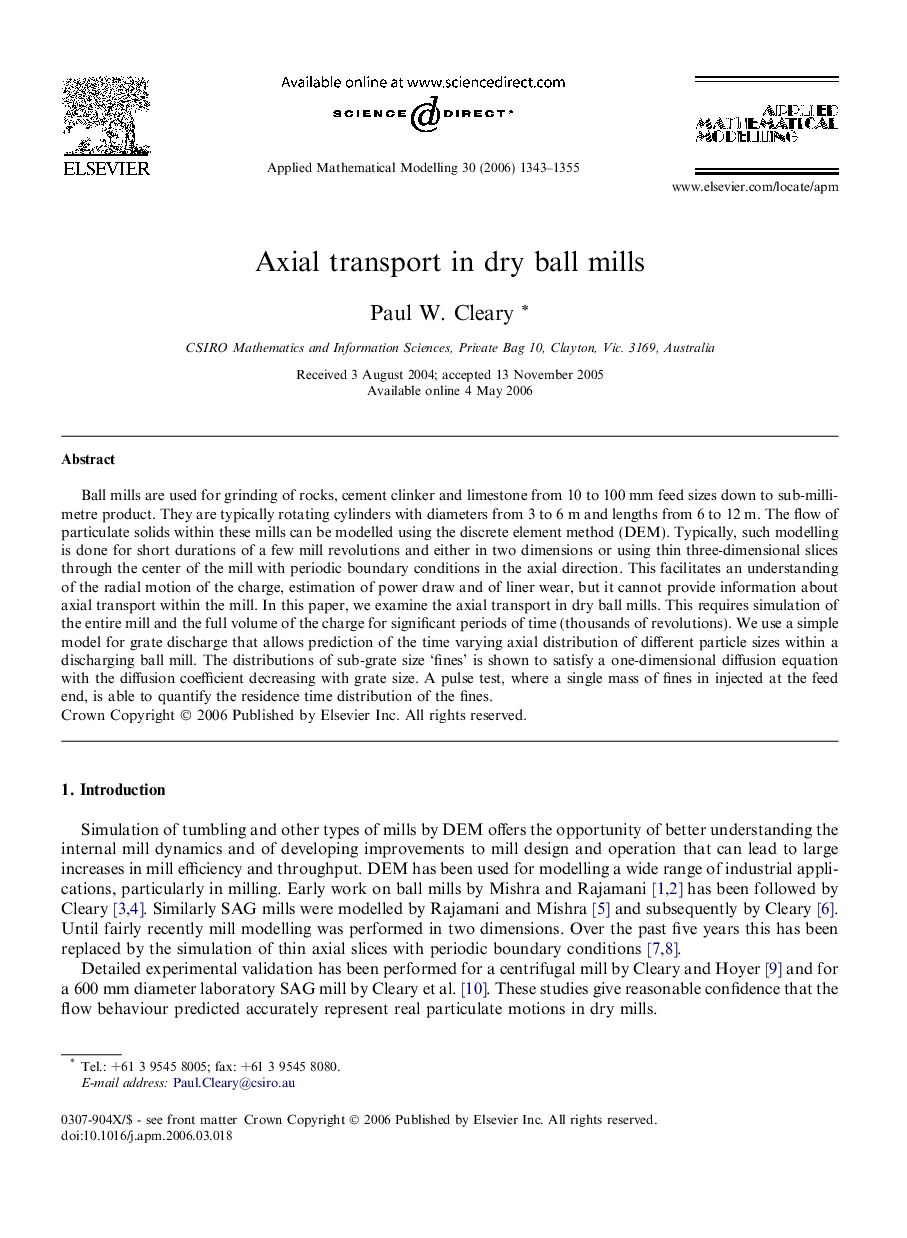
Ball mills are used for grinding of rocks, cement clinker and limestone from 10 to 100 mm feed sizes down to sub-millimetre product. They are typically rotating cylinders with diameters from 3 to 6 m and lengths from 6 to 12 m. The flow of particulate solids within these mills can be modelled using the discrete element method (DEM). Typically, such modelling is done for short durations of a few mill revolutions and either in two dimensions or using thin three-dimensional slices through the center of the mill with periodic boundary conditions in the axial direction. This facilitates an understanding of the radial motion of the charge, estimation of power draw and of liner wear, but it cannot provide information about axial transport within the mill. In this paper, we examine the axial transport in dry ball mills. This requires simulation of the entire mill and the full volume of the charge for significant periods of time (thousands of revolutions). We use a simple model for grate discharge that allows prediction of the time varying axial distribution of different particle sizes within a discharging ball mill. The distributions of sub-grate size ‘fines’ is shown to satisfy a one-dimensional diffusion equation with the diffusion coefficient decreasing with grate size. A pulse test, where a single mass of fines in injected at the feed end, is able to quantify the residence time distribution of the fines.
Journal: Applied Mathematical Modelling - Volume 30, Issue 11, November 2006, Pages 1343–1355