کد مقاله | کد نشریه | سال انتشار | مقاله انگلیسی | نسخه تمام متن |
---|---|---|---|---|
1707322 | 1012543 | 2006 | 22 صفحه PDF | دانلود رایگان |
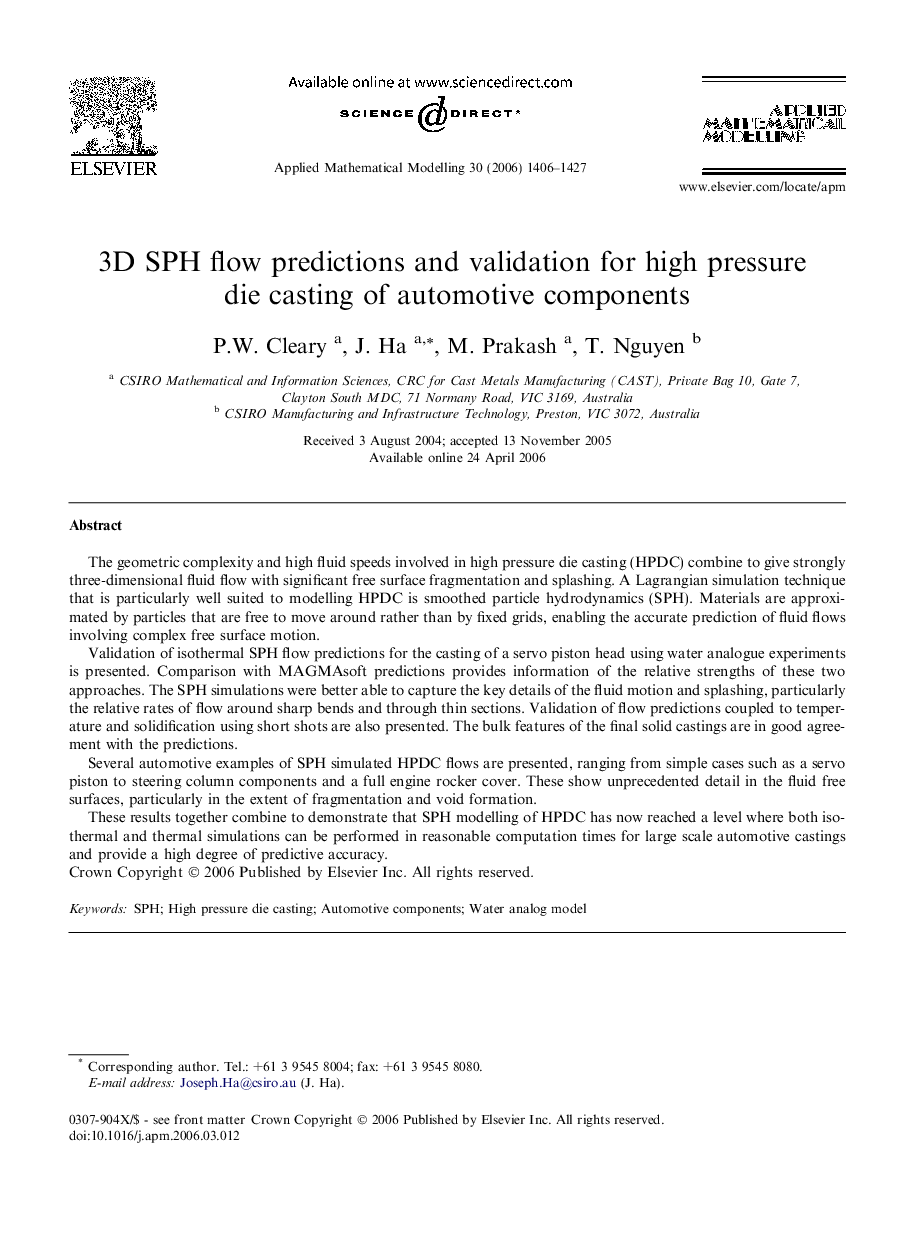
The geometric complexity and high fluid speeds involved in high pressure die casting (HPDC) combine to give strongly three-dimensional fluid flow with significant free surface fragmentation and splashing. A Lagrangian simulation technique that is particularly well suited to modelling HPDC is smoothed particle hydrodynamics (SPH). Materials are approximated by particles that are free to move around rather than by fixed grids, enabling the accurate prediction of fluid flows involving complex free surface motion.Validation of isothermal SPH flow predictions for the casting of a servo piston head using water analogue experiments is presented. Comparison with MAGMAsoft predictions provides information of the relative strengths of these two approaches. The SPH simulations were better able to capture the key details of the fluid motion and splashing, particularly the relative rates of flow around sharp bends and through thin sections. Validation of flow predictions coupled to temperature and solidification using short shots are also presented. The bulk features of the final solid castings are in good agreement with the predictions.Several automotive examples of SPH simulated HPDC flows are presented, ranging from simple cases such as a servo piston to steering column components and a full engine rocker cover. These show unprecedented detail in the fluid free surfaces, particularly in the extent of fragmentation and void formation.These results together combine to demonstrate that SPH modelling of HPDC has now reached a level where both isothermal and thermal simulations can be performed in reasonable computation times for large scale automotive castings and provide a high degree of predictive accuracy.
Journal: Applied Mathematical Modelling - Volume 30, Issue 11, November 2006, Pages 1406–1427