کد مقاله | کد نشریه | سال انتشار | مقاله انگلیسی | نسخه تمام متن |
---|---|---|---|---|
542748 | 1450365 | 2014 | 5 صفحه PDF | دانلود رایگان |
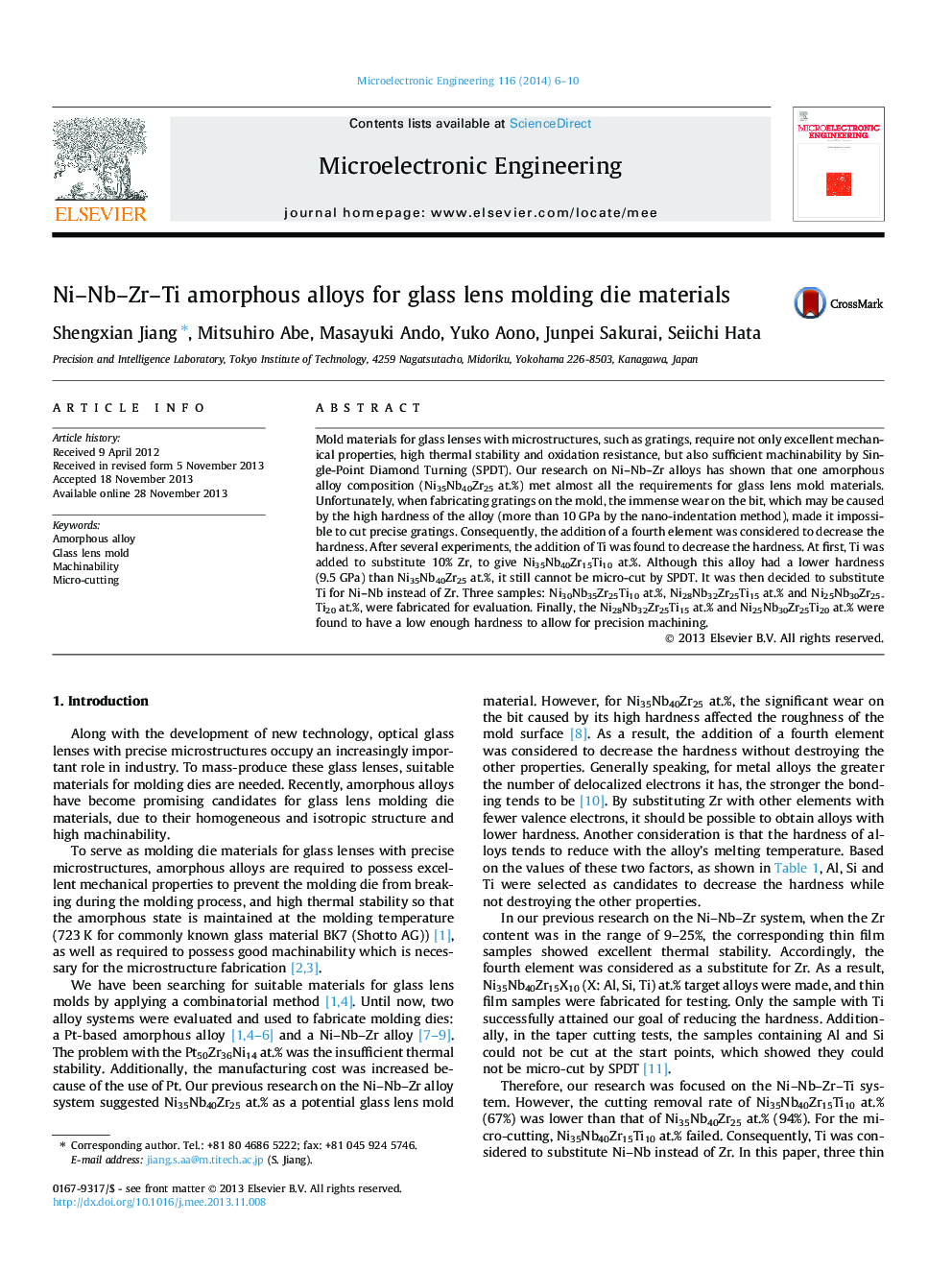
• We add the forth element Ti to Ni–Nb–Zr alloy system to improve micro-machinability.
• The addition of Ti does decrease the hardness.
• Ni28Nb32Zr25Ti15 at.% and Ni25Nb30Zr25Ti20 at.% are successful to be micro-cut.
• The sample with Ti content level 20 at.% has the best result for micro-cutting.
• Better machinability might be expected by further increasing Ti content level.
Mold materials for glass lenses with microstructures, such as gratings, require not only excellent mechanical properties, high thermal stability and oxidation resistance, but also sufficient machinability by Single-Point Diamond Turning (SPDT). Our research on Ni–Nb–Zr alloys has shown that one amorphous alloy composition (Ni35Nb40Zr25 at.%) met almost all the requirements for glass lens mold materials. Unfortunately, when fabricating gratings on the mold, the immense wear on the bit, which may be caused by the high hardness of the alloy (more than 10 GPa by the nano-indentation method), made it impossible to cut precise gratings. Consequently, the addition of a fourth element was considered to decrease the hardness. After several experiments, the addition of Ti was found to decrease the hardness. At first, Ti was added to substitute 10% Zr, to give Ni35Nb40Zr15Ti10 at.%. Although this alloy had a lower hardness (9.5 GPa) than Ni35Nb40Zr25 at.%, it still cannot be micro-cut by SPDT. It was then decided to substitute Ti for Ni–Nb instead of Zr. Three samples: Ni30Nb35Zr25Ti10 at.%, Ni28Nb32Zr25Ti15 at.% and Ni25Nb30Zr25Ti20 at.%, were fabricated for evaluation. Finally, the Ni28Nb32Zr25Ti15 at.% and Ni25Nb30Zr25Ti20 at.% were found to have a low enough hardness to allow for precision machining.
Figure optionsDownload as PowerPoint slide
Journal: Microelectronic Engineering - Volume 116, 25 March 2014, Pages 6–10