کد مقاله | کد نشریه | سال انتشار | مقاله انگلیسی | نسخه تمام متن |
---|---|---|---|---|
615809 | 881461 | 2010 | 6 صفحه PDF | دانلود رایگان |
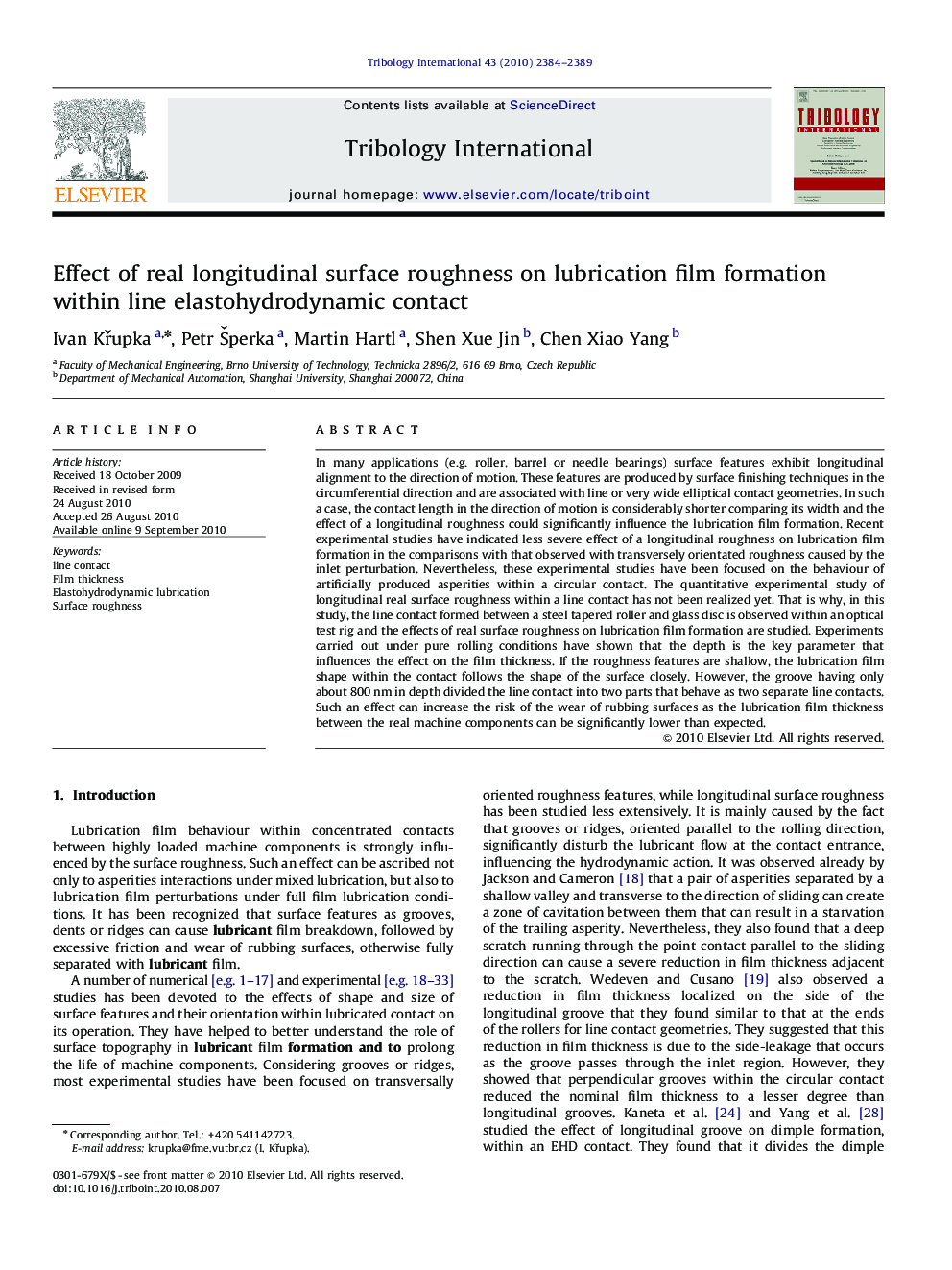
In many applications (e.g. roller, barrel or needle bearings) surface features exhibit longitudinal alignment to the direction of motion. These features are produced by surface finishing techniques in the circumferential direction and are associated with line or very wide elliptical contact geometries. In such a case, the contact length in the direction of motion is considerably shorter comparing its width and the effect of a longitudinal roughness could significantly influence the lubrication film formation. Recent experimental studies have indicated less severe effect of a longitudinal roughness on lubrication film formation in the comparisons with that observed with transversely orientated roughness caused by the inlet perturbation. Nevertheless, these experimental studies have been focused on the behaviour of artificially produced asperities within a circular contact. The quantitative experimental study of longitudinal real surface roughness within a line contact has not been realized yet. That is why, in this study, the line contact formed between a steel tapered roller and glass disc is observed within an optical test rig and the effects of real surface roughness on lubrication film formation are studied. Experiments carried out under pure rolling conditions have shown that the depth is the key parameter that influences the effect on the film thickness. If the roughness features are shallow, the lubrication film shape within the contact follows the shape of the surface closely. However, the groove having only about 800 nm in depth divided the line contact into two parts that behave as two separate line contacts. Such an effect can increase the risk of the wear of rubbing surfaces as the lubrication film thickness between the real machine components can be significantly lower than expected.
Research highlights
► Longitudinal groove depth is key parameter that influences effect on film thickness.
► Lubrication film follows shape of surface having shallow logitudinal features closely.
► Deep groove divides line contact into two parts that behave as two separate contacts.
► Reduction of lubricant film thickness increases risk of rubbing surfaces wear.
Journal: Tribology International - Volume 43, Issue 12, December 2010, Pages 2384–2389