کد مقاله | کد نشریه | سال انتشار | مقاله انگلیسی | نسخه تمام متن |
---|---|---|---|---|
6454418 | 1418817 | 2017 | 13 صفحه PDF | دانلود رایگان |
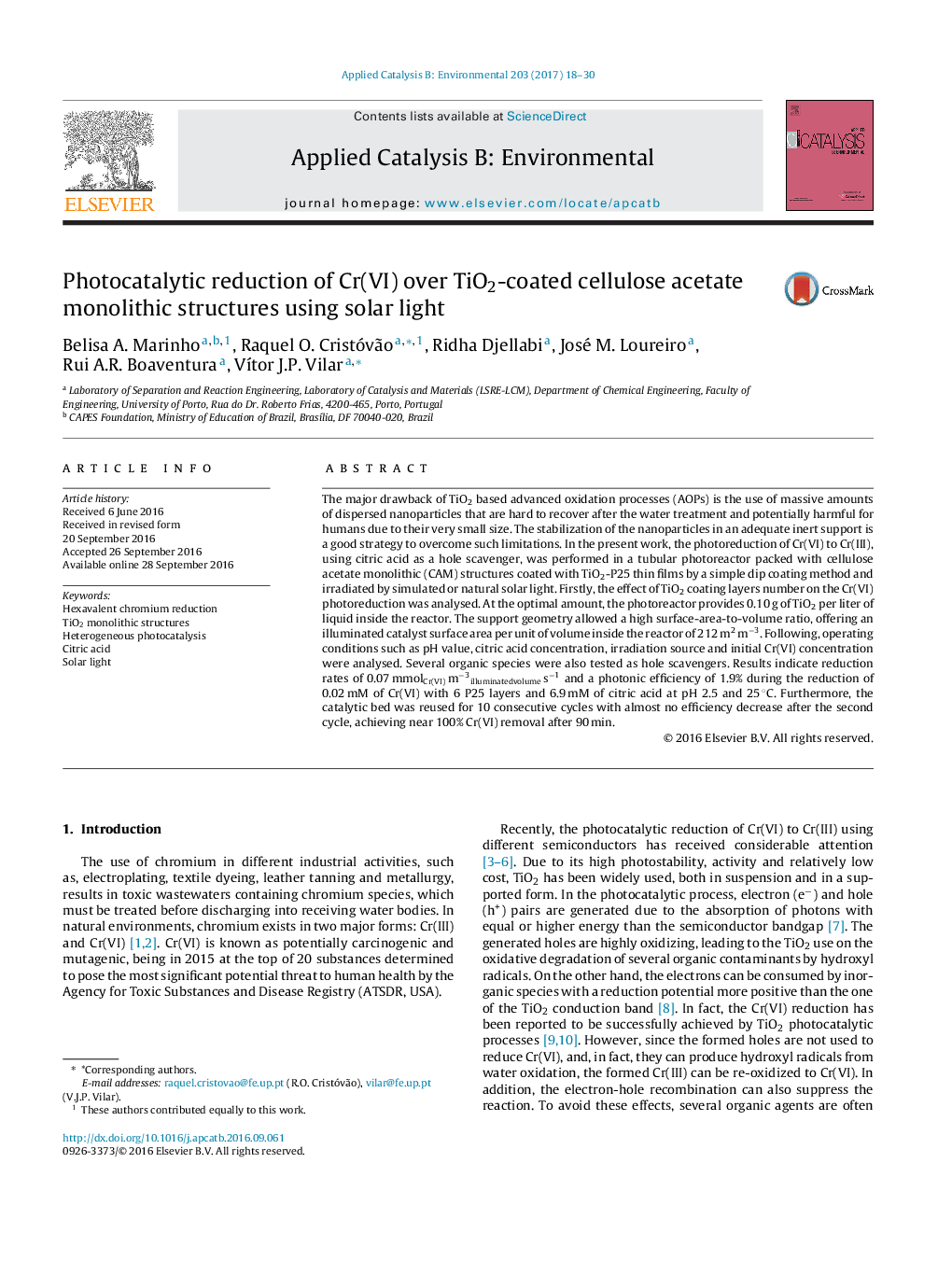
- Cellulose acetate monoliths coated with TiO2 were used for Cr(VI) photoreduction.
- The presence of citric acid enhanced Cr(VI) reduction by TiO2/UVA-vis system.
- The support allows an illuminated catalyst surface area per volume of 212Â m2Â mâ3.
- The higher reduction rates were achieved with 6.9Â mM of citric acid at pH 2.5.
- The immobilized TiO2 proved to be suitable for the continuous Cr(VI) reduction.
The major drawback of TiO2 based advanced oxidation processes (AOPs) is the use of massive amounts of dispersed nanoparticles that are hard to recover after the water treatment and potentially harmful for humans due to their very small size. The stabilization of the nanoparticles in an adequate inert support is a good strategy to overcome such limitations. In the present work, the photoreduction of Cr(VI) to Cr(III), using citric acid as a hole scavenger, was performed in a tubular photoreactor packed with cellulose acetate monolithic (CAM) structures coated with TiO2-P25 thin films by a simple dip coating method and irradiated by simulated or natural solar light. Firstly, the effect of TiO2 coating layers number on the Cr(VI) photoreduction was analysed. At the optimal amount, the photoreactor provides 0.10 g of TiO2 per liter of liquid inside the reactor. The support geometry allowed a high surface-area-to-volume ratio, offering an illuminated catalyst surface area per unit of volume inside the reactor of 212 m2 mâ3. Following, operating conditions such as pH value, citric acid concentration, irradiation source and initial Cr(VI) concentration were analysed. Several organic species were also tested as hole scavengers. Results indicate reduction rates of 0.07 mmolCr(VI) mâ3illuminatedvolume sâ1 and a photonic efficiency of 1.9% during the reduction of 0.02 mM of Cr(VI) with 6 P25 layers and 6.9 mM of citric acid at pH 2.5 and 25 °C. Furthermore, the catalytic bed was reused for 10 consecutive cycles with almost no efficiency decrease after the second cycle, achieving near 100% Cr(VI) removal after 90 min.
241
Journal: Applied Catalysis B: Environmental - Volume 203, April 2017, Pages 18-30