کد مقاله | کد نشریه | سال انتشار | مقاله انگلیسی | نسخه تمام متن |
---|---|---|---|---|
763358 | 1462970 | 2015 | 6 صفحه PDF | دانلود رایگان |
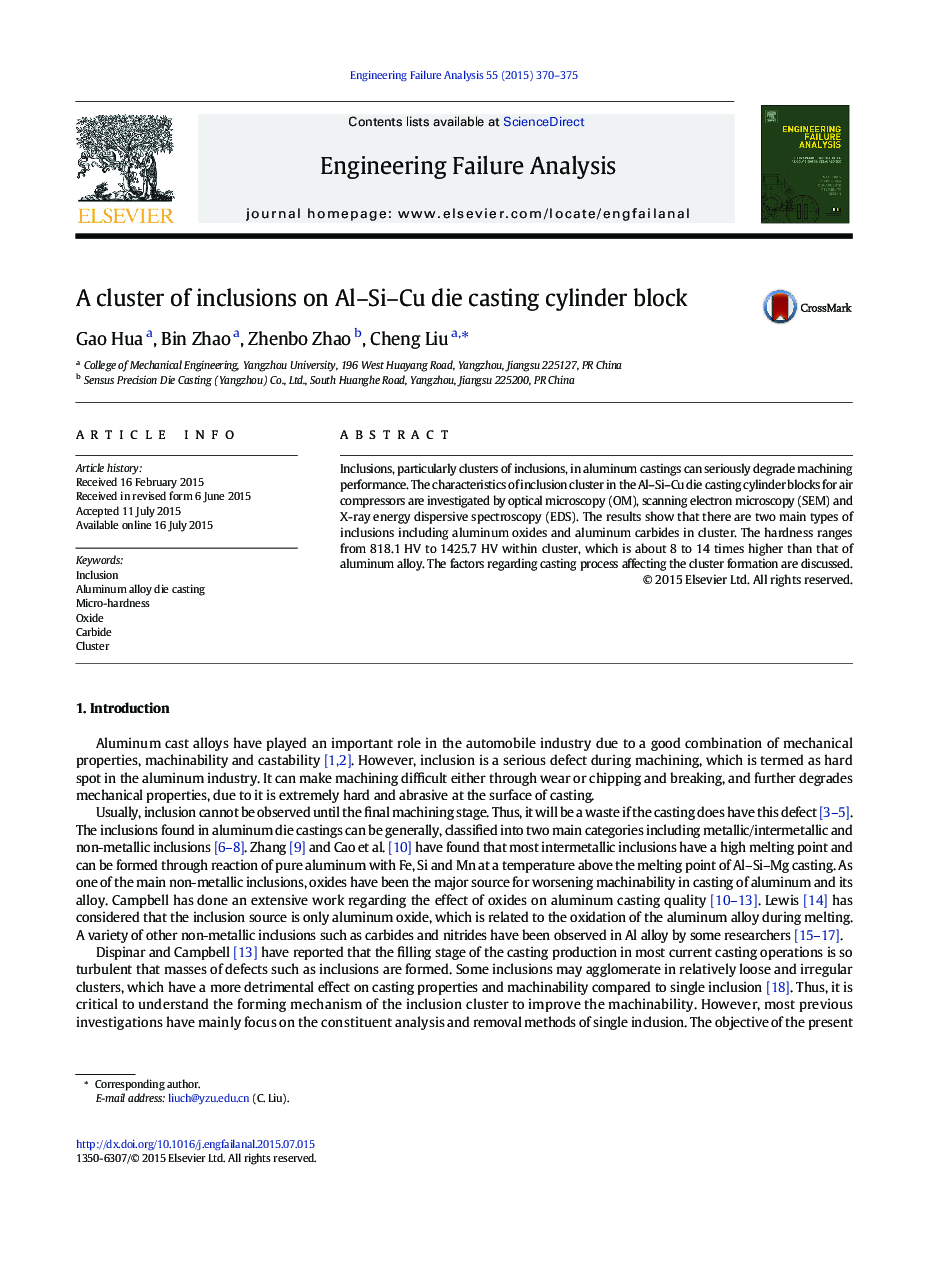
• In casting process, some inclusions in aluminum liquid may agglomerate in relatively loose and irregular clusters, which have a more detrimental effect on casting properties and machinability than single inclusion.
• The characteristics of an inclusion cluster in the Al-Si-Cu die casting cylinder blocks for air compressors are investigated.
• The results show that there are two main types of hard spots including Al2O3 and Al4C3 in cluster.
• The hardness ranges from 818.1HV to 1425.7HV within hard spot cluster, which is considerable higher than that of aluminum alloy.
• The aluminum oxides are mainly formed during pouring.
• The cause of generation of aluminum carbide is primarily attributed to the filling of shot tip oil for lubricating both plunger and shot sleeve during die casting process.
Inclusions, particularly clusters of inclusions, in aluminum castings can seriously degrade machining performance. The characteristics of inclusion cluster in the Al–Si–Cu die casting cylinder blocks for air compressors are investigated by optical microscopy (OM), scanning electron microscopy (SEM) and X-ray energy dispersive spectroscopy (EDS). The results show that there are two main types of inclusions including aluminum oxides and aluminum carbides in cluster. The hardness ranges from 818.1 HV to 1425.7 HV within cluster, which is about 8 to 14 times higher than that of aluminum alloy. The factors regarding casting process affecting the cluster formation are discussed.
Journal: Engineering Failure Analysis - Volume 55, September 2015, Pages 370–375