کد مقاله | کد نشریه | سال انتشار | مقاله انگلیسی | نسخه تمام متن |
---|---|---|---|---|
763647 | 896944 | 2011 | 8 صفحه PDF | دانلود رایگان |
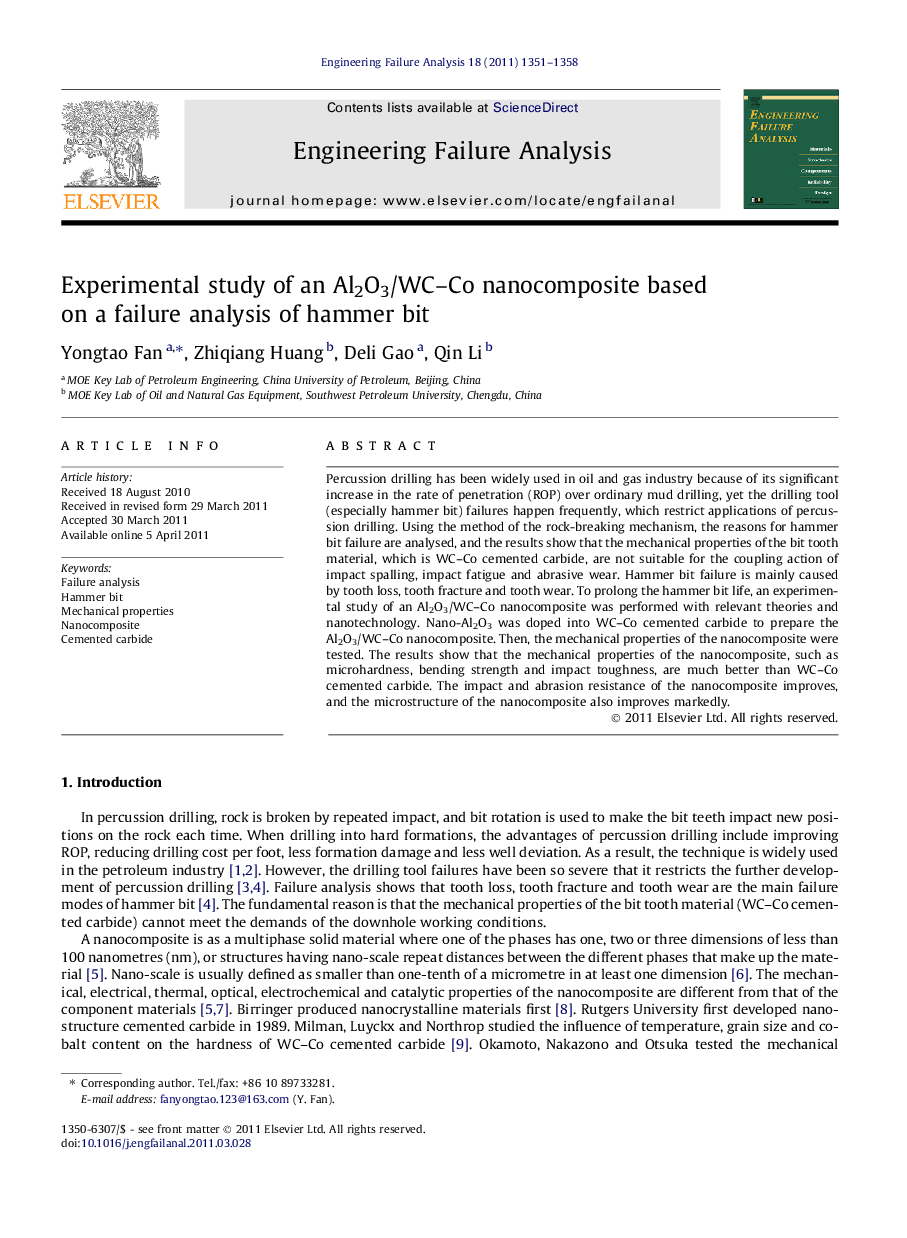
Percussion drilling has been widely used in oil and gas industry because of its significant increase in the rate of penetration (ROP) over ordinary mud drilling, yet the drilling tool (especially hammer bit) failures happen frequently, which restrict applications of percussion drilling. Using the method of the rock-breaking mechanism, the reasons for hammer bit failure are analysed, and the results show that the mechanical properties of the bit tooth material, which is WC–Co cemented carbide, are not suitable for the coupling action of impact spalling, impact fatigue and abrasive wear. Hammer bit failure is mainly caused by tooth loss, tooth fracture and tooth wear. To prolong the hammer bit life, an experimental study of an Al2O3/WC–Co nanocomposite was performed with relevant theories and nanotechnology. Nano-Al2O3 was doped into WC–Co cemented carbide to prepare the Al2O3/WC–Co nanocomposite. Then, the mechanical properties of the nanocomposite were tested. The results show that the mechanical properties of the nanocomposite, such as microhardness, bending strength and impact toughness, are much better than WC–Co cemented carbide. The impact and abrasion resistance of the nanocomposite improves, and the microstructure of the nanocomposite also improves markedly.
► Hammer bit failure is mainly caused by tooth loss, tooth fracture and tooth wear.
► The mechanical properties of bit tooth material (WC–Co cemented carbide) are inadequate.
► To prolong the life of hammer bit, a study of an Al2O3/WC–Co nanocomposite was conducted.
► The mechanical properties of the Al2O3/WC–Co are much better than those of WC–Co cemented carbide.
► The Al2O3/WC–Co is suitable as a hammer bit tooth material in percussion drilling.
Journal: Engineering Failure Analysis - Volume 18, Issue 5, July 2011, Pages 1351–1358