کد مقاله | کد نشریه | سال انتشار | مقاله انگلیسی | نسخه تمام متن |
---|---|---|---|---|
769621 | 1462979 | 2014 | 16 صفحه PDF | دانلود رایگان |
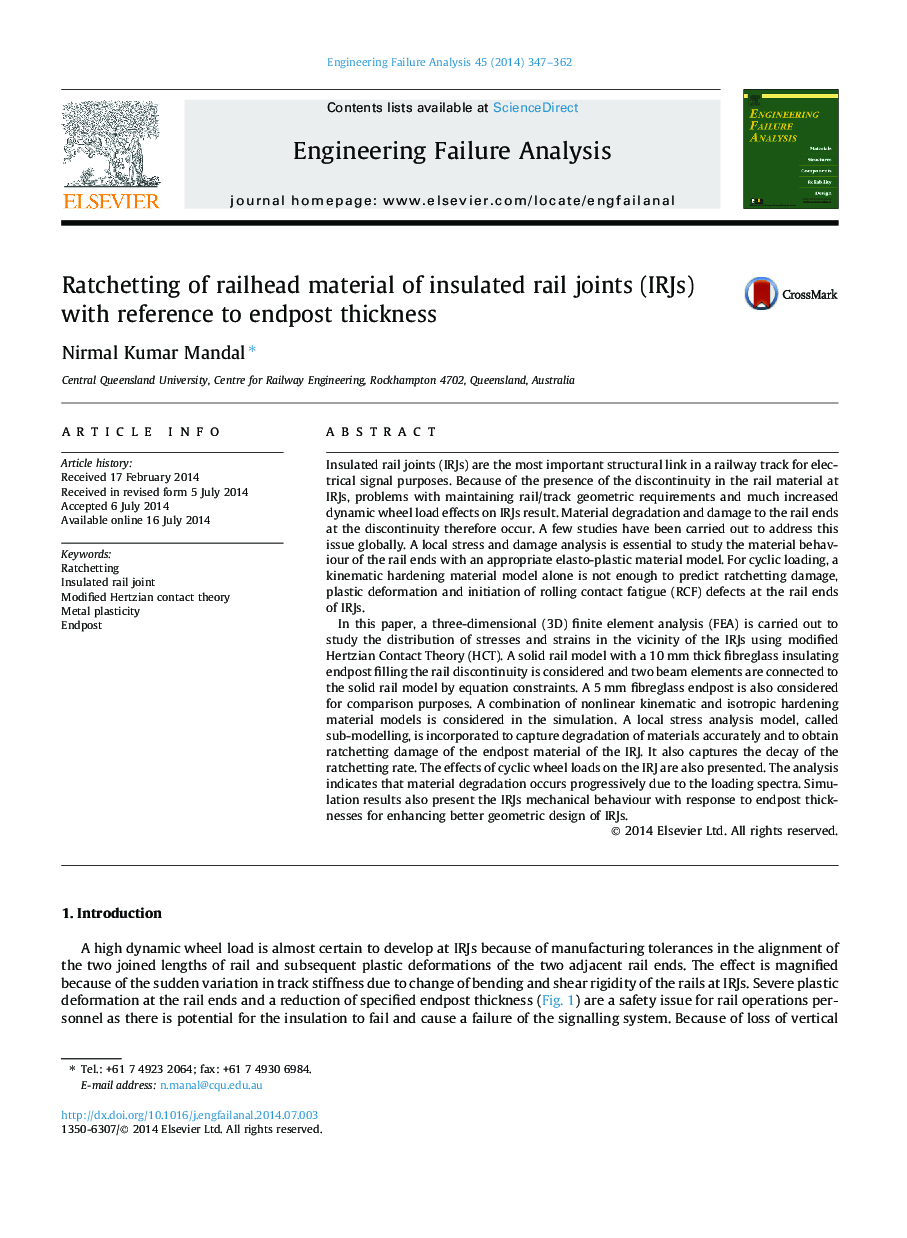
• A thicker endpost joint is more prone to progressive IRJ railhead material damage.
• A 5 mm thick endpost can improve fatigue behaviour of railhead material as compared to a 10 mm thick endpost.
• Maximum residual stresses are at the subsurface about 2–3 mm depth on the railhead end face.
• The most influential stress component for surface damage and for subsurface damage is von-Mises stress.
Insulated rail joints (IRJs) are the most important structural link in a railway track for electrical signal purposes. Because of the presence of the discontinuity in the rail material at IRJs, problems with maintaining rail/track geometric requirements and much increased dynamic wheel load effects on IRJs result. Material degradation and damage to the rail ends at the discontinuity therefore occur. A few studies have been carried out to address this issue globally. A local stress and damage analysis is essential to study the material behaviour of the rail ends with an appropriate elasto-plastic material model. For cyclic loading, a kinematic hardening material model alone is not enough to predict ratchetting damage, plastic deformation and initiation of rolling contact fatigue (RCF) defects at the rail ends of IRJs.In this paper, a three-dimensional (3D) finite element analysis (FEA) is carried out to study the distribution of stresses and strains in the vicinity of the IRJs using modified Hertzian Contact Theory (HCT). A solid rail model with a 10 mm thick fibreglass insulating endpost filling the rail discontinuity is considered and two beam elements are connected to the solid rail model by equation constraints. A 5 mm fibreglass endpost is also considered for comparison purposes. A combination of nonlinear kinematic and isotropic hardening material models is considered in the simulation. A local stress analysis model, called sub-modelling, is incorporated to capture degradation of materials accurately and to obtain ratchetting damage of the endpost material of the IRJ. It also captures the decay of the ratchetting rate. The effects of cyclic wheel loads on the IRJ are also presented. The analysis indicates that material degradation occurs progressively due to the loading spectra. Simulation results also present the IRJs mechanical behaviour with response to endpost thicknesses for enhancing better geometric design of IRJs.
Journal: Engineering Failure Analysis - Volume 45, October 2014, Pages 347–362