کد مقاله | کد نشریه | سال انتشار | مقاله انگلیسی | نسخه تمام متن |
---|---|---|---|---|
769669 | 1463007 | 2008 | 21 صفحه PDF | دانلود رایگان |
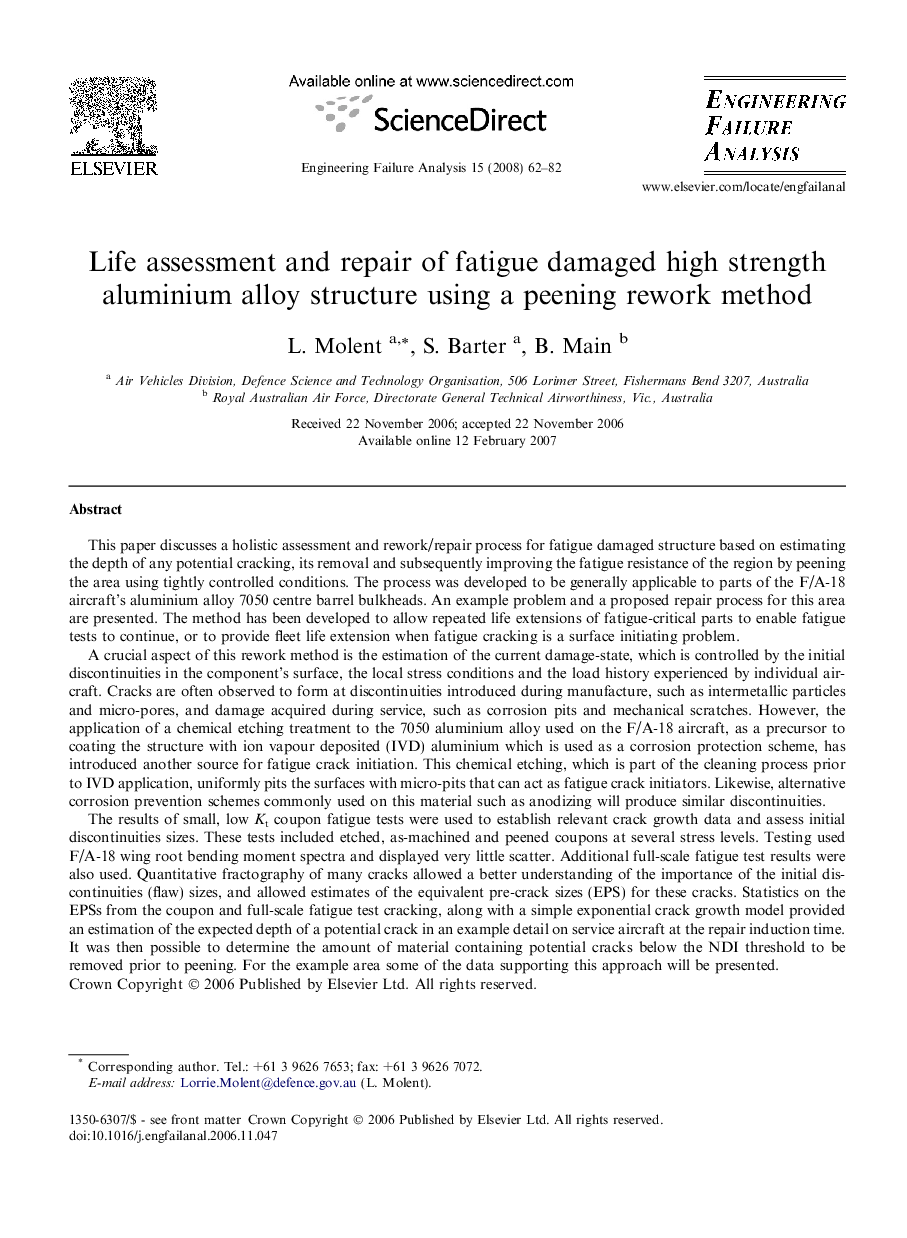
This paper discusses a holistic assessment and rework/repair process for fatigue damaged structure based on estimating the depth of any potential cracking, its removal and subsequently improving the fatigue resistance of the region by peening the area using tightly controlled conditions. The process was developed to be generally applicable to parts of the F/A-18 aircraft’s aluminium alloy 7050 centre barrel bulkheads. An example problem and a proposed repair process for this area are presented. The method has been developed to allow repeated life extensions of fatigue-critical parts to enable fatigue tests to continue, or to provide fleet life extension when fatigue cracking is a surface initiating problem.A crucial aspect of this rework method is the estimation of the current damage-state, which is controlled by the initial discontinuities in the component’s surface, the local stress conditions and the load history experienced by individual aircraft. Cracks are often observed to form at discontinuities introduced during manufacture, such as intermetallic particles and micro-pores, and damage acquired during service, such as corrosion pits and mechanical scratches. However, the application of a chemical etching treatment to the 7050 aluminium alloy used on the F/A-18 aircraft, as a precursor to coating the structure with ion vapour deposited (IVD) aluminium which is used as a corrosion protection scheme, has introduced another source for fatigue crack initiation. This chemical etching, which is part of the cleaning process prior to IVD application, uniformly pits the surfaces with micro-pits that can act as fatigue crack initiators. Likewise, alternative corrosion prevention schemes commonly used on this material such as anodizing will produce similar discontinuities.The results of small, low Kt coupon fatigue tests were used to establish relevant crack growth data and assess initial discontinuities sizes. These tests included etched, as-machined and peened coupons at several stress levels. Testing used F/A-18 wing root bending moment spectra and displayed very little scatter. Additional full-scale fatigue test results were also used. Quantitative fractography of many cracks allowed a better understanding of the importance of the initial discontinuities (flaw) sizes, and allowed estimates of the equivalent pre-crack sizes (EPS) for these cracks. Statistics on the EPSs from the coupon and full-scale fatigue test cracking, along with a simple exponential crack growth model provided an estimation of the expected depth of a potential crack in an example detail on service aircraft at the repair induction time. It was then possible to determine the amount of material containing potential cracks below the NDI threshold to be removed prior to peening. For the example area some of the data supporting this approach will be presented.
Journal: Engineering Failure Analysis - Volume 15, Issues 1–2, January–March 2008, Pages 62–82