کد مقاله | کد نشریه | سال انتشار | مقاله انگلیسی | نسخه تمام متن |
---|---|---|---|---|
769867 | 1463004 | 2012 | 8 صفحه PDF | دانلود رایگان |
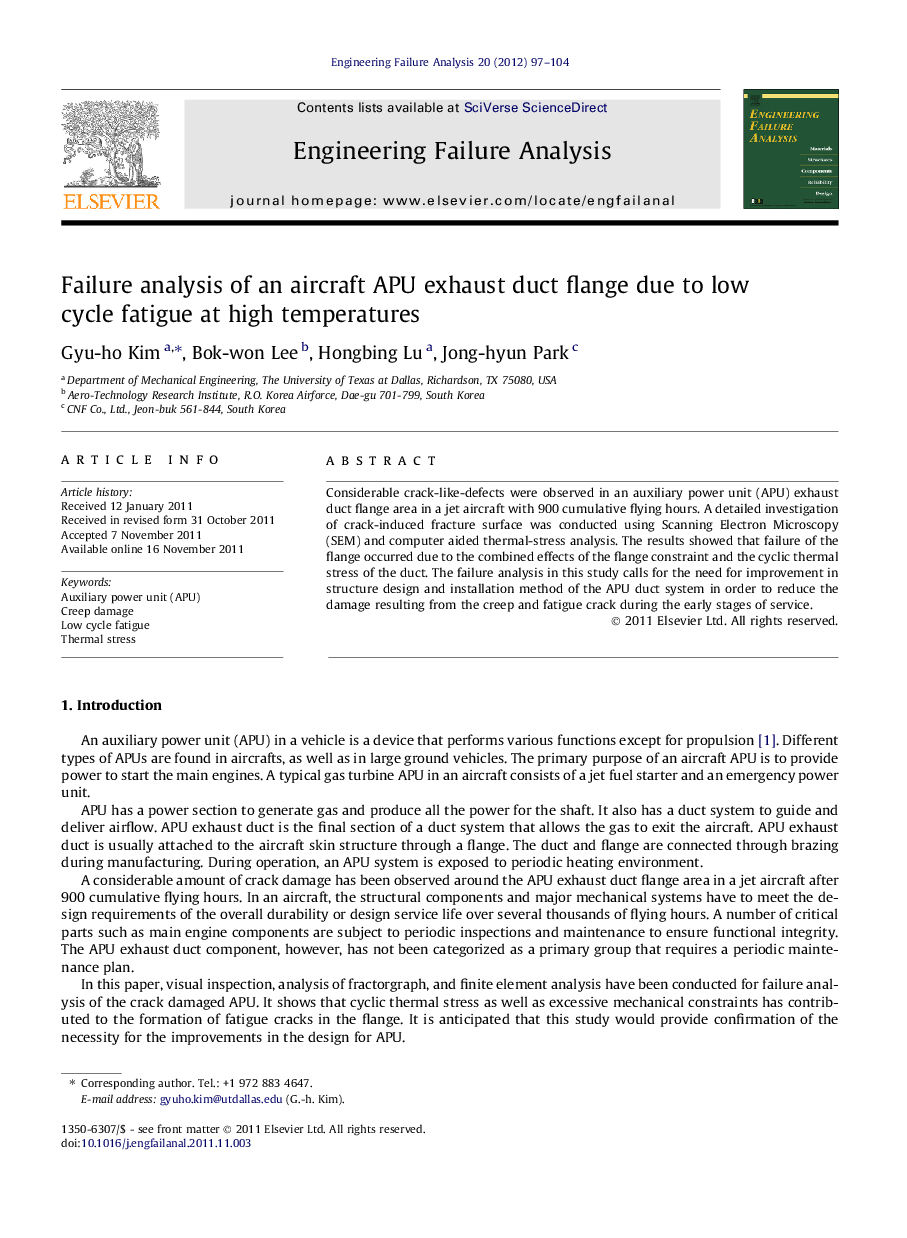
Considerable crack-like-defects were observed in an auxiliary power unit (APU) exhaust duct flange area in a jet aircraft with 900 cumulative flying hours. A detailed investigation of crack-induced fracture surface was conducted using Scanning Electron Microscopy (SEM) and computer aided thermal-stress analysis. The results showed that failure of the flange occurred due to the combined effects of the flange constraint and the cyclic thermal stress of the duct. The failure analysis in this study calls for the need for improvement in structure design and installation method of the APU duct system in order to reduce the damage resulting from the creep and fatigue crack during the early stages of service.
► Investigation into the failure of an aircraft APU duct revealed that mechanical constraint and thermal expansion are main causes for the failure.
► The duct flange was exposed to creep and fatigue situations with high thermal stress during the APU system operation.
► FEA based analysis strongly supported the investigation results.
Journal: Engineering Failure Analysis - Volume 20, March 2012, Pages 97–104