کد مقاله | کد نشریه | سال انتشار | مقاله انگلیسی | نسخه تمام متن |
---|---|---|---|---|
770126 | 897460 | 2007 | 12 صفحه PDF | دانلود رایگان |
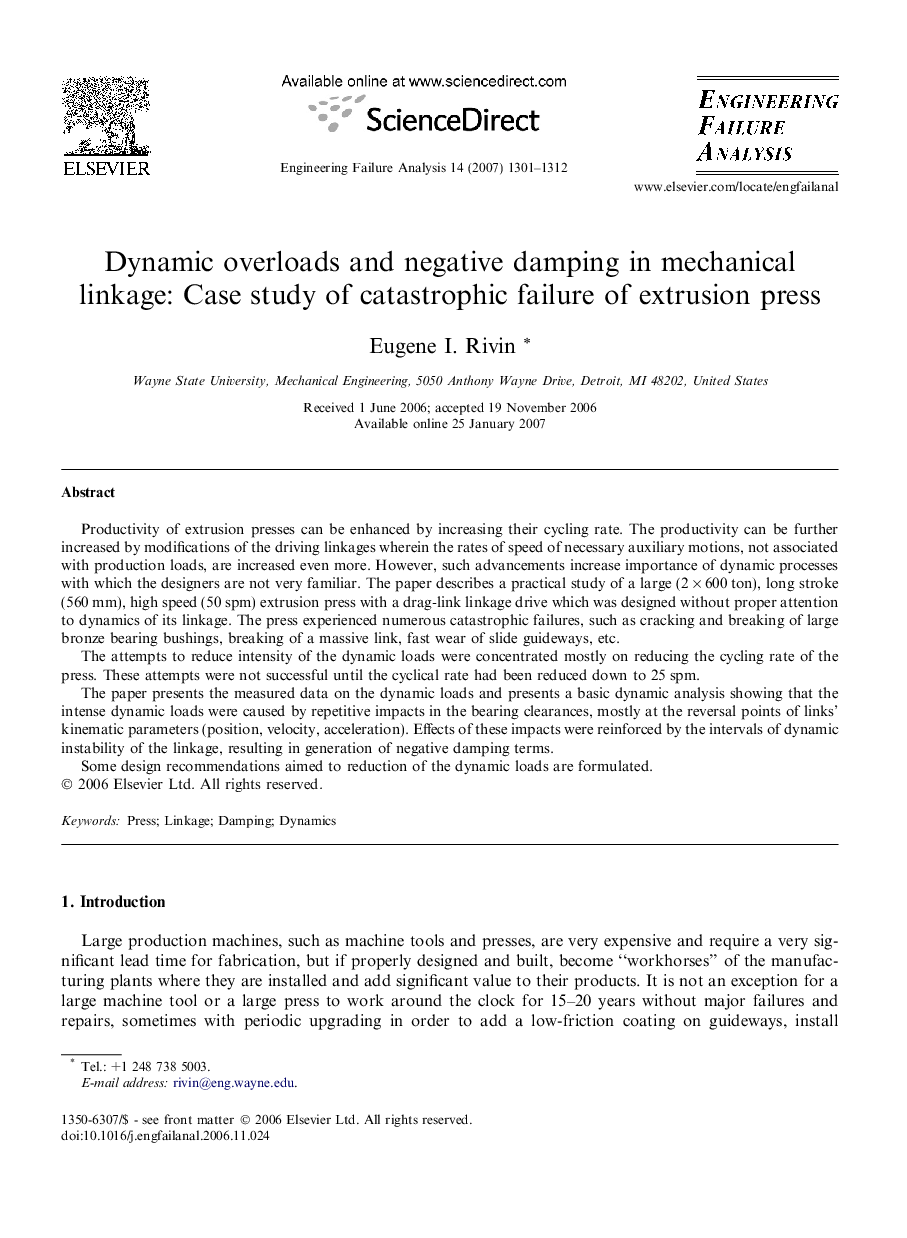
Productivity of extrusion presses can be enhanced by increasing their cycling rate. The productivity can be further increased by modifications of the driving linkages wherein the rates of speed of necessary auxiliary motions, not associated with production loads, are increased even more. However, such advancements increase importance of dynamic processes with which the designers are not very familiar. The paper describes a practical study of a large (2 × 600 ton), long stroke (560 mm), high speed (50 spm) extrusion press with a drag-link linkage drive which was designed without proper attention to dynamics of its linkage. The press experienced numerous catastrophic failures, such as cracking and breaking of large bronze bearing bushings, breaking of a massive link, fast wear of slide guideways, etc.The attempts to reduce intensity of the dynamic loads were concentrated mostly on reducing the cycling rate of the press. These attempts were not successful until the cyclical rate had been reduced down to 25 spm.The paper presents the measured data on the dynamic loads and presents a basic dynamic analysis showing that the intense dynamic loads were caused by repetitive impacts in the bearing clearances, mostly at the reversal points of links’ kinematic parameters (position, velocity, acceleration). Effects of these impacts were reinforced by the intervals of dynamic instability of the linkage, resulting in generation of negative damping terms.Some design recommendations aimed to reduction of the dynamic loads are formulated.
Journal: Engineering Failure Analysis - Volume 14, Issue 7, October 2007, Pages 1301–1312