کد مقاله | کد نشریه | سال انتشار | مقاله انگلیسی | نسخه تمام متن |
---|---|---|---|---|
1180619 | 1491538 | 2015 | 14 صفحه PDF | دانلود رایگان |
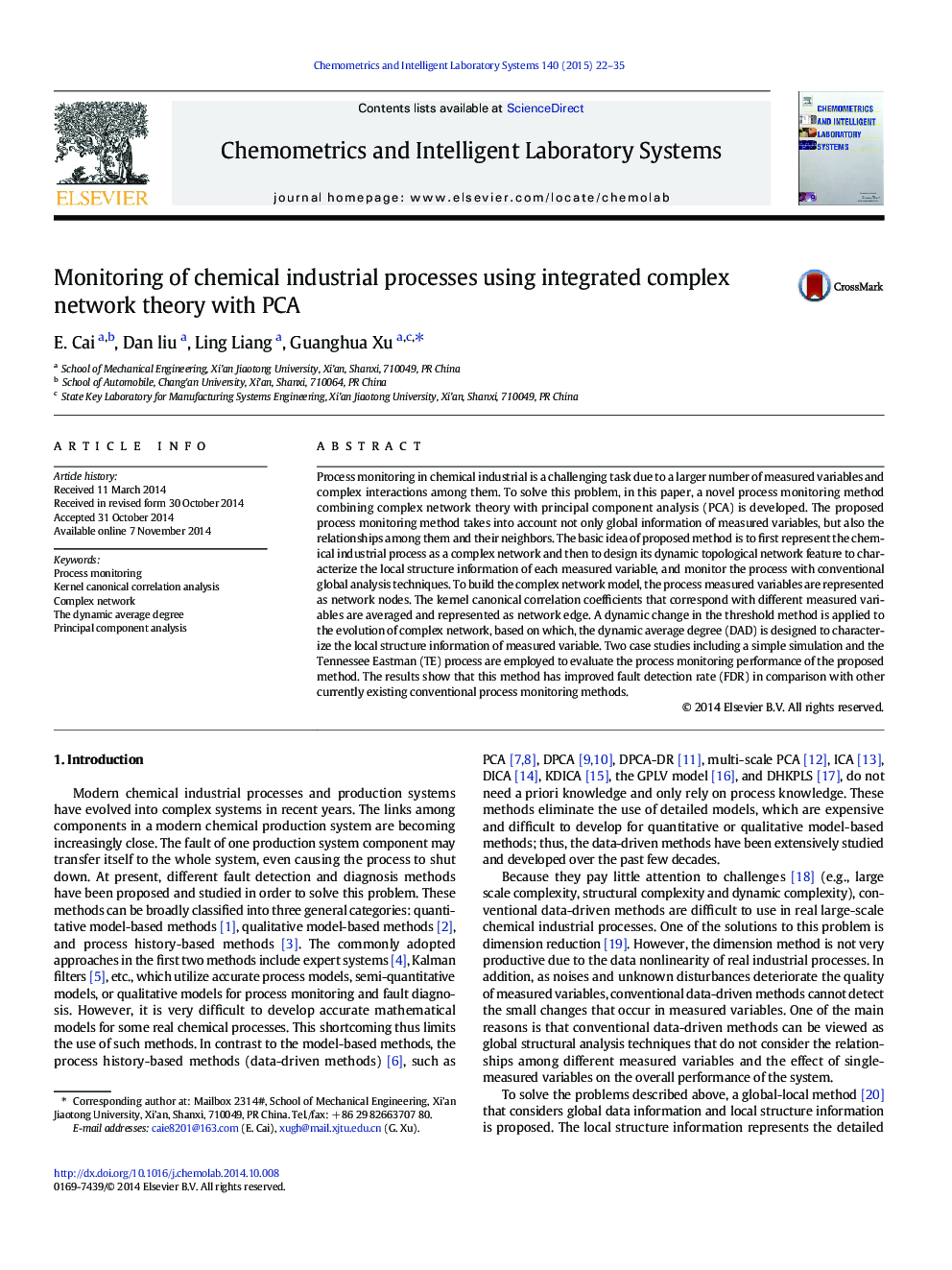
• The process measured variables are represented as network nodes. Kernel canonical correlation coefficient corresponding to different measured variables is averaged and represented as network edge. A chemical industrial process based on complex network theory is modeled.
• A dynamic change of threshold method is applied to the evolution of complex network, based on which, the dynamic average degree (DAD) is designed to characterize the local information of measured variable. The results of experiment show that the proposed DAD is sensitive to the fault and helpful for identification of fault variables.
Process monitoring in chemical industrial is a challenging task due to a larger number of measured variables and complex interactions among them. To solve this problem, in this paper, a novel process monitoring method combining complex network theory with principal component analysis (PCA) is developed. The proposed process monitoring method takes into account not only global information of measured variables, but also the relationships among them and their neighbors. The basic idea of proposed method is to first represent the chemical industrial process as a complex network and then to design its dynamic topological network feature to characterize the local structure information of each measured variable, and monitor the process with conventional global analysis techniques. To build the complex network model, the process measured variables are represented as network nodes. The kernel canonical correlation coefficients that correspond with different measured variables are averaged and represented as network edge. A dynamic change in the threshold method is applied to the evolution of complex network, based on which, the dynamic average degree (DAD) is designed to characterize the local structure information of measured variable. Two case studies including a simple simulation and the Tennessee Eastman (TE) process are employed to evaluate the process monitoring performance of the proposed method. The results show that this method has improved fault detection rate (FDR) in comparison with other currently existing conventional process monitoring methods.
Journal: Chemometrics and Intelligent Laboratory Systems - Volume 140, 15 January 2015, Pages 22–35