کد مقاله | کد نشریه | سال انتشار | مقاله انگلیسی | نسخه تمام متن |
---|---|---|---|---|
190251 | 459695 | 2011 | 6 صفحه PDF | دانلود رایگان |
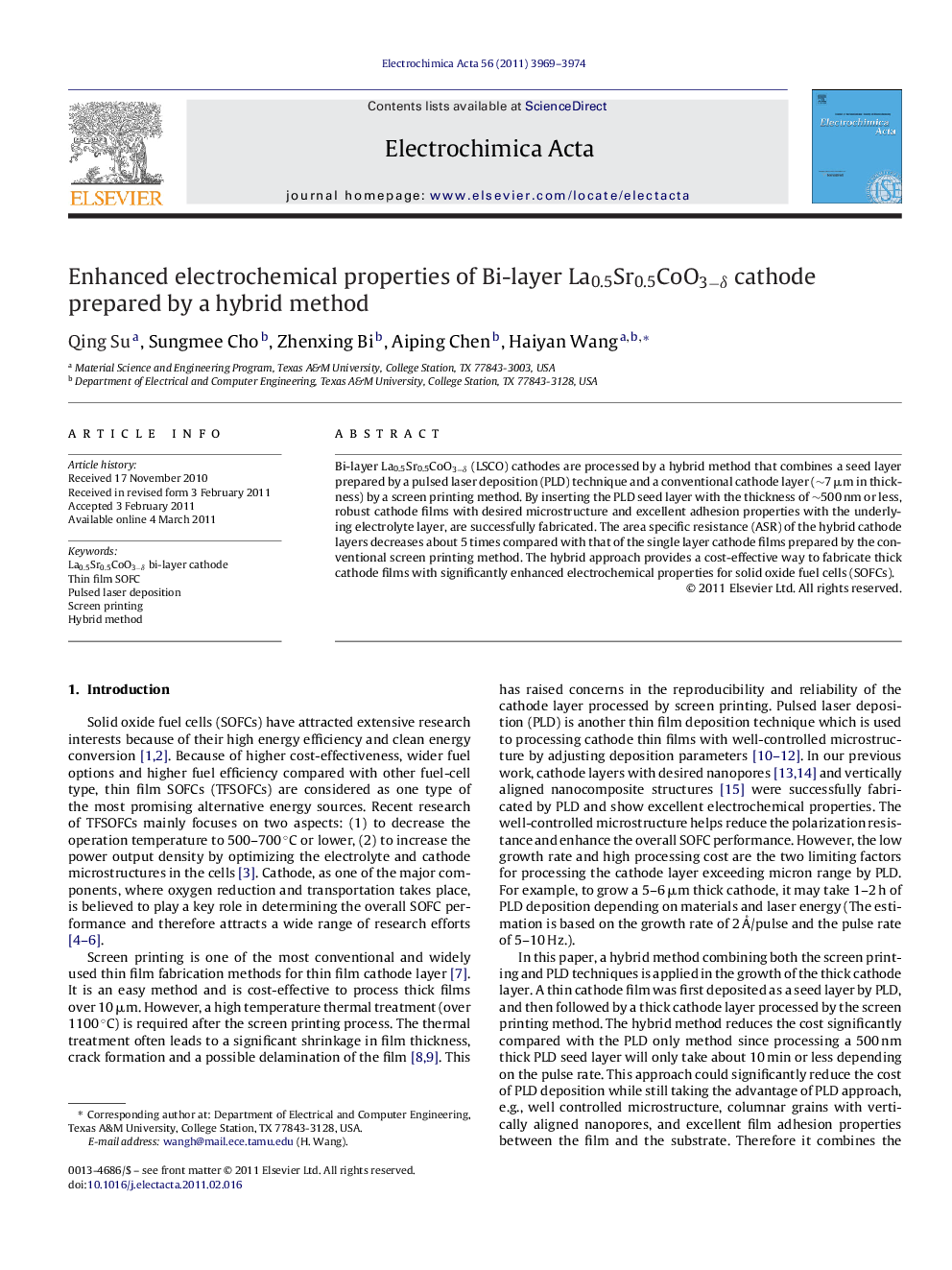
Bi-layer La0.5Sr0.5CoO3−δ (LSCO) cathodes are processed by a hybrid method that combines a seed layer prepared by a pulsed laser deposition (PLD) technique and a conventional cathode layer (∼7 μm in thickness) by a screen printing method. By inserting the PLD seed layer with the thickness of ∼500 nm or less, robust cathode films with desired microstructure and excellent adhesion properties with the underlying electrolyte layer, are successfully fabricated. The area specific resistance (ASR) of the hybrid cathode layers decreases about 5 times compared with that of the single layer cathode films prepared by the conventional screen printing method. The hybrid approach provides a cost-effective way to fabricate thick cathode films with significantly enhanced electrochemical properties for solid oxide fuel cells (SOFCs).
(A) Cross-section TEM image of the bilayer LSCO cathode prepared by the hybrid of screen printing and PLD techniques. The hybrid method combines the advantages of both deposition techniques. (B) The area specific resistance (ASR) of the hybrid cathode layers decreases about 5 times compared with that of the single layer cathode films prepared by the conventional screen printing method.Figure optionsDownload as PowerPoint slideResearch highlights
► Bi-layer cathodes are processed by pulsed laser deposition and screen printing methods.
► Better electrochemical and mechanical properties in the bi-layer cathodes are observed.
► No delamination or crack formation in the bi-layer films was found after thermal cycles.
► The hybrid method offers a cost-effective way in fabricating thick and high quality cathode films.
Journal: Electrochimica Acta - Volume 56, Issue 11, 15 April 2011, Pages 3969–3974