کد مقاله | کد نشریه | سال انتشار | مقاله انگلیسی | نسخه تمام متن |
---|---|---|---|---|
211924 | 462025 | 2015 | 7 صفحه PDF | دانلود رایگان |
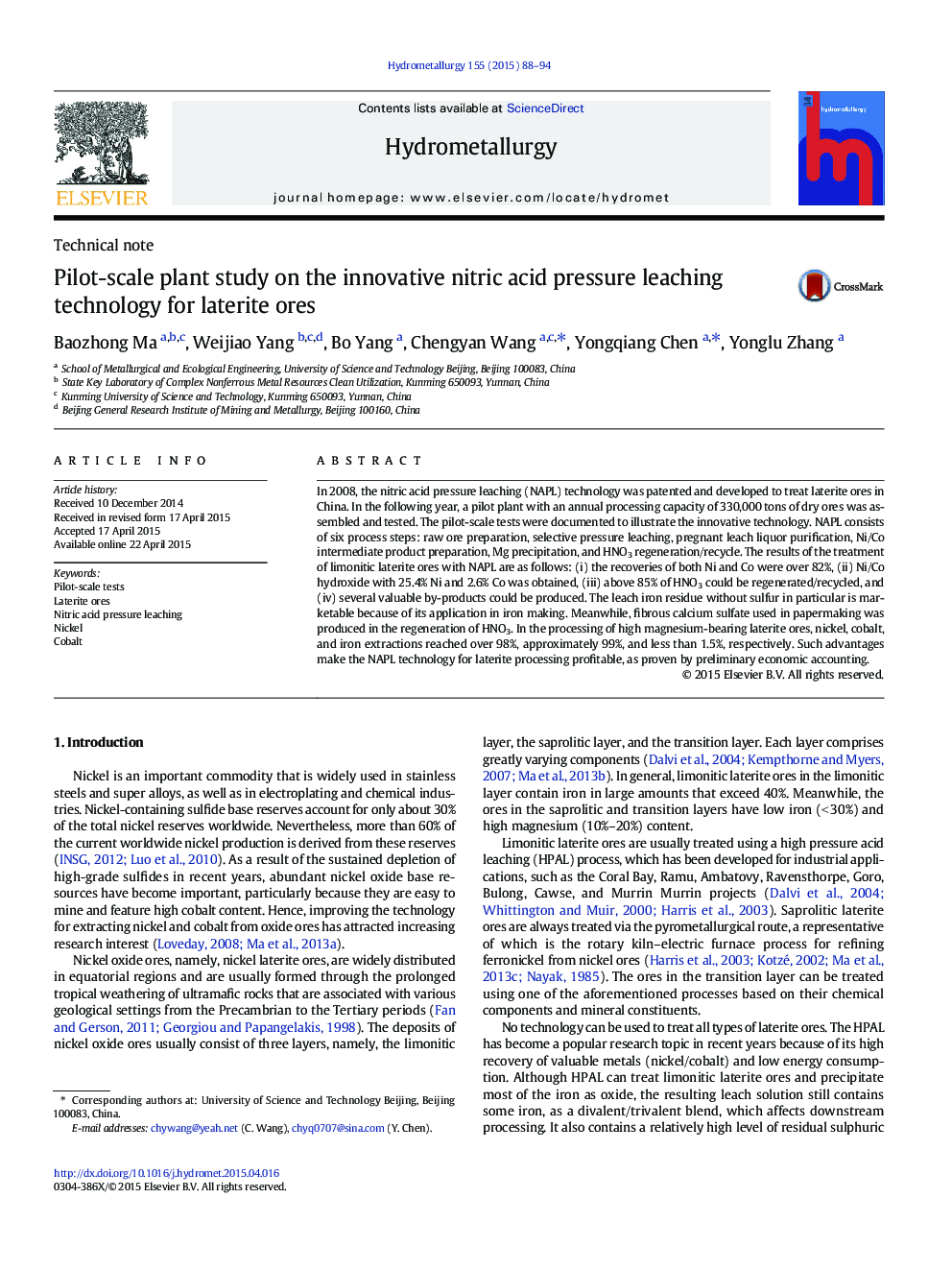
• Nitric acid pressure leaching was developed for processing all types of laterite.
• Pilot plant was assembled and the pilot-scale tests were carried out.
• Results of the tests were summarized to illustrate all processes of this technology.
• Several obtained valuable by-products can enhance competitiveness of the technology.
In 2008, the nitric acid pressure leaching (NAPL) technology was patented and developed to treat laterite ores in China. In the following year, a pilot plant with an annual processing capacity of 330,000 tons of dry ores was assembled and tested. The pilot-scale tests were documented to illustrate the innovative technology. NAPL consists of six process steps: raw ore preparation, selective pressure leaching, pregnant leach liquor purification, Ni/Co intermediate product preparation, Mg precipitation, and HNO3 regeneration/recycle. The results of the treatment of limonitic laterite ores with NAPL are as follows: (i) the recoveries of both Ni and Co were over 82%, (ii) Ni/Co hydroxide with 25.4% Ni and 2.6% Co was obtained, (iii) above 85% of HNO3 could be regenerated/recycled, and (iv) several valuable by-products could be produced. The leach iron residue without sulfur in particular is marketable because of its application in iron making. Meanwhile, fibrous calcium sulfate used in papermaking was produced in the regeneration of HNO3. In the processing of high magnesium-bearing laterite ores, nickel, cobalt, and iron extractions reached over 98%, approximately 99%, and less than 1.5%, respectively. Such advantages make the NAPL technology for laterite processing profitable, as proven by preliminary economic accounting.
Figure optionsDownload as PowerPoint slide
Journal: Hydrometallurgy - Volume 155, May 2015, Pages 88–94