کد مقاله | کد نشریه | سال انتشار | مقاله انگلیسی | نسخه تمام متن |
---|---|---|---|---|
7044675 | 1457086 | 2018 | 31 صفحه PDF | دانلود رایگان |
عنوان انگلیسی مقاله ISI
Metal 3D-printed wick structures for heat pipe application: Capillary performance analysis
دانلود مقاله + سفارش ترجمه
دانلود مقاله ISI انگلیسی
رایگان برای ایرانیان
کلمات کلیدی
موضوعات مرتبط
مهندسی و علوم پایه
مهندسی شیمی
جریان سیال و فرایندهای انتقال
پیش نمایش صفحه اول مقاله
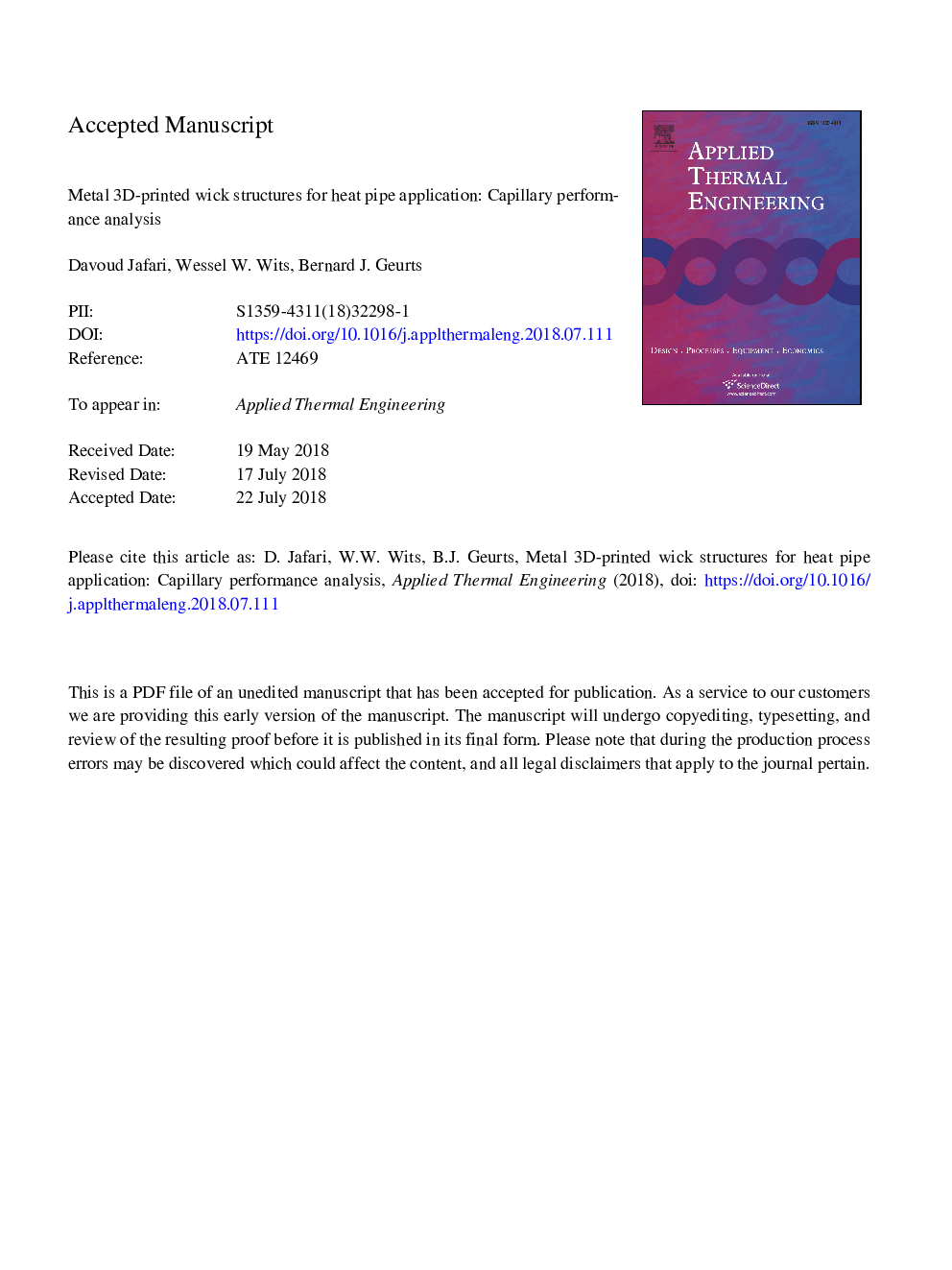
چکیده انگلیسی
This paper examines the so-called capillary performance of a freeform porous structure fabricated by advanced 3D metal printing technology. The fabricated structure is intended as wick for two-phase heat transfer devices, in which it contributes to the transport of a liquid working fluid through capillary forces. A stainless steel porous structure is additively manufactured and characterized in terms of its porosity (ε), effective pore radius (reff), liquid permeability (K) and capillary performance (K/reff). Forced liquid flow tests with deionized water as working fluid are conducted to determine the permeability. Capillary penetration experiments are performed by means of height-time (h-t) and weight-time (w-t) techniques with different fluids to characterize the capillary performance of the printed wicks. The experimentally determined values of permeability and pressure drop are compared with the well-known Darcy's law and Forchheimer corrections. The Kozeny-Carman correlation is found to predict the experimental values of permeability at lower flow velocities (0.07â¯m/s corresponding to a Reynolds number of 0.95), while at higher velocities an under-prediction of the experimental data is observed. The Kozeny-like model taking into account inertial effects is updated in terms of constant values that fit with the experimental data very well. The accuracy of the theoretical models for characterizing capillary rate-or-rise processes is also assessed. It is concluded that the capillary penetration of liquids in the 3D-printed wick follows the law: h(t)â¯â¼ t1/3 at intermediate stage. Observation confirms that the gravitational effect played a significant role in the 3D-printed wick, introducing slower capillary rising. Compared to sintered powder, screen mesh and composite wicks selected from literature, the designed 3D-printed wick enhances the capillary performance. It is concluded that due to the large permeability and capillary performance (K/reff), heat pipes in conjunction with a 3D-printed wick can significantly augment their heat transfer.
ناشر
Database: Elsevier - ScienceDirect (ساینس دایرکت)
Journal: Applied Thermal Engineering - Volume 143, October 2018, Pages 403-414
Journal: Applied Thermal Engineering - Volume 143, October 2018, Pages 403-414
نویسندگان
Davoud Jafari, Wessel W. Wits, Bernard J. Geurts,