کد مقاله | کد نشریه | سال انتشار | مقاله انگلیسی | نسخه تمام متن |
---|---|---|---|---|
768228 | 1462967 | 2016 | 8 صفحه PDF | دانلود رایگان |
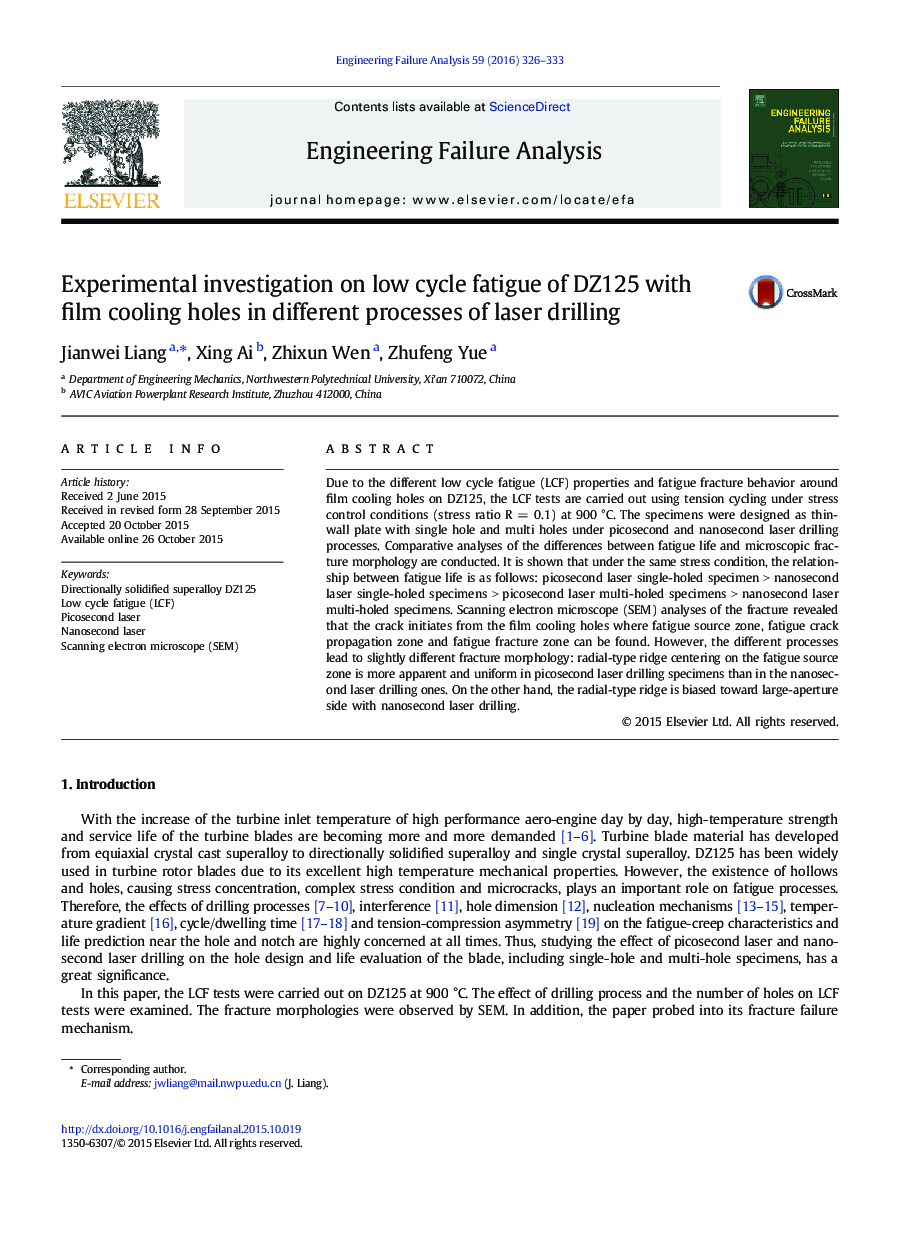
Highlight
• Low cycle fatigue tests are carried out under stress control conditions.
• The specimens were designed as thin-wall plate with single hole and multi holes.
• The processes of laser drilling are chosen picosecond laser and nanosecond laser.
• Emphasis is placed on the differences between fatigue life and microscopic fracture morphology.
• Picosecond laser single-holed specimens has the longest life.
Due to the different low cycle fatigue (LCF) properties and fatigue fracture behavior around film cooling holes on DZ125, the LCF tests are carried out using tension cycling under stress control conditions (stress ratio R = 0.1) at 900 °C. The specimens were designed as thin-wall plate with single hole and multi holes under picosecond and nanosecond laser drilling processes. Comparative analyses of the differences between fatigue life and microscopic fracture morphology are conducted. It is shown that under the same stress condition, the relationship between fatigue life is as follows: picosecond laser single-holed specimen > nanosecond laser single-holed specimens > picosecond laser multi-holed specimens > nanosecond laser multi-holed specimens. Scanning electron microscope (SEM) analyses of the fracture revealed that the crack initiates from the film cooling holes where fatigue source zone, fatigue crack propagation zone and fatigue fracture zone can be found. However, the different processes lead to slightly different fracture morphology: radial-type ridge centering on the fatigue source zone is more apparent and uniform in picosecond laser drilling specimens than in the nanosecond laser drilling ones. On the other hand, the radial-type ridge is biased toward large-aperture side with nanosecond laser drilling.
Journal: Engineering Failure Analysis - Volume 59, January 2016, Pages 326–333