کد مقاله | کد نشریه | سال انتشار | مقاله انگلیسی | نسخه تمام متن |
---|---|---|---|---|
1664393 | 1008756 | 2015 | 8 صفحه PDF | دانلود رایگان |
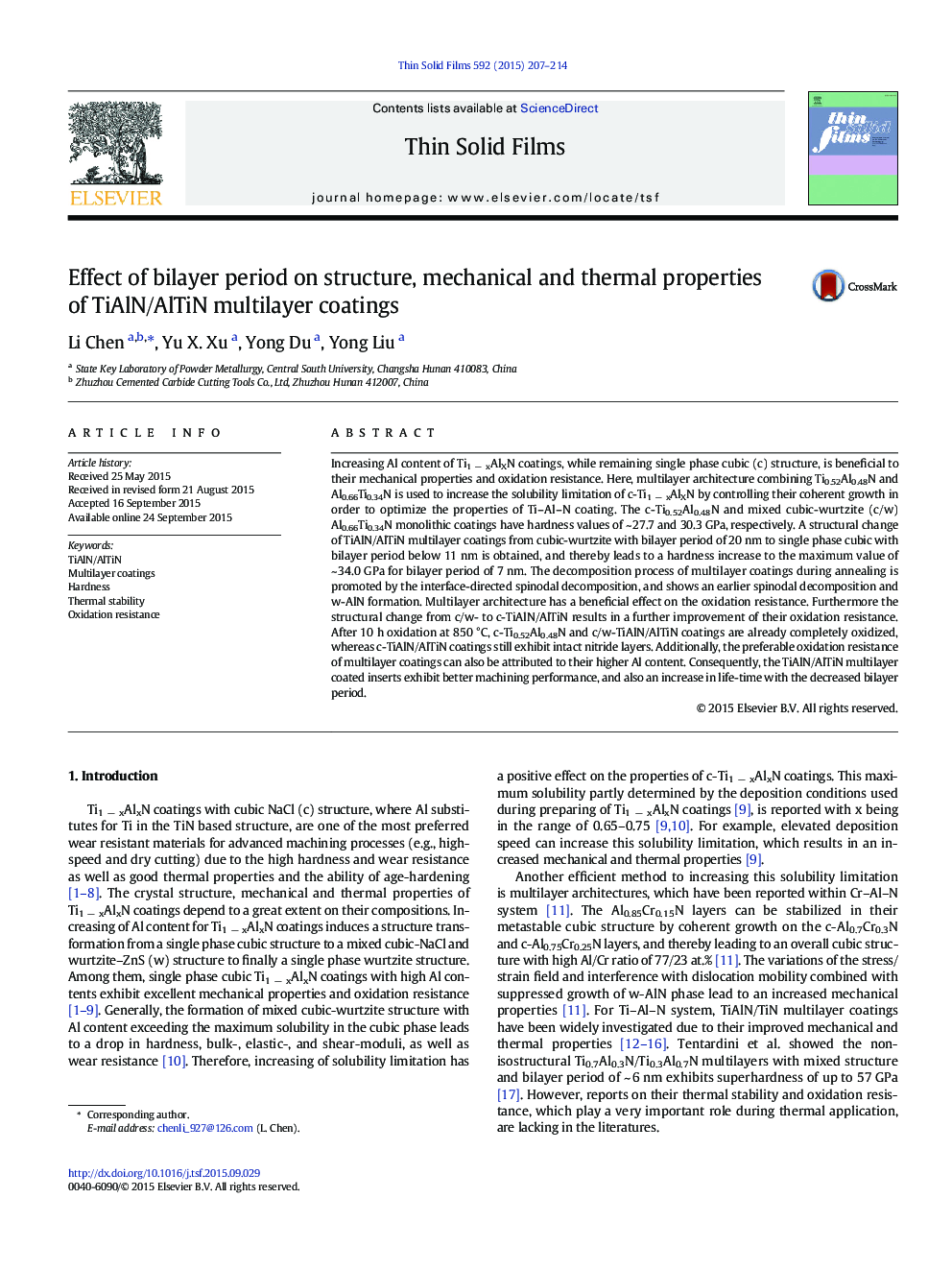
• TiAlN/AlTiN coatings combining Ti0.52Al0.48N and Al0.66Ti0.34N layers are prepared.
• Decreasing bilayer period causes a structural change from cubic-wurtzite to cubic.
• Multilayer architecture leads to an increased hardness and oxidation resistance.
• Multilayer architecture promotes the thermal decomposition process of Ti–Al–N.
• TiAlN/AlTiN multilayer coatings behave better machining performance.
Increasing Al content of Ti1 − xAlXN coatings, while remaining single phase cubic (c) structure, is beneficial to their mechanical properties and oxidation resistance. Here, multilayer architecture combining Ti0.52Al0.48N and Al0.66Ti0.34N is used to increase the solubility limitation of c-Ti1 − xAlXN by controlling their coherent growth in order to optimize the properties of Ti–Al–N coating. The c-Ti0.52Al0.48N and mixed cubic-wurtzite (c/w) Al0.66Ti0.34N monolithic coatings have hardness values of ~ 27.7 and 30.3 GPa, respectively. A structural change of TiAlN/AlTiN multilayer coatings from cubic-wurtzite with bilayer period of 20 nm to single phase cubic with bilayer period below 11 nm is obtained, and thereby leads to a hardness increase to the maximum value of ~ 34.0 GPa for bilayer period of 7 nm. The decomposition process of multilayer coatings during annealing is promoted by the interface-directed spinodal decomposition, and shows an earlier spinodal decomposition and w-AlN formation. Multilayer architecture has a beneficial effect on the oxidation resistance. Furthermore the structural change from c/w- to c-TiAlN/AlTiN results in a further improvement of their oxidation resistance. After 10 h oxidation at 850 °C, c-Ti0.52Al0.48N and c/w-TiAlN/AlTiN coatings are already completely oxidized, whereas c-TiAlN/AlTiN coatings still exhibit intact nitride layers. Additionally, the preferable oxidation resistance of multilayer coatings can also be attributed to their higher Al content. Consequently, the TiAlN/AlTiN multilayer coated inserts exhibit better machining performance, and also an increase in life-time with the decreased bilayer period.
Journal: Thin Solid Films - Volume 592, Part A, 1 October 2015, Pages 207–214